StrEng007
Structural
- Aug 22, 2014
- 543
I don’t know the best way to go about introducing this topic, so I’ll give a specific scenario before I try to explain the applicable part of ACI Chapter 17.
Let’s say you have a load that is being dragged along a concrete beam and you’re providing post installed anchors to resolve that loading. In this scenario the beam is an 8”x24” concrete beam, and the anchors are provided along the centerline of the 8” dimension (top of beam).
The governing load failure for a single anchor in shear (parallel to length of beam) ends up being concrete edge breakout. This can achieve a strength design reaction of 2,000 lb.
Per Hilti Profis analysis, when providing groups of anchors loaded in the same scenario, the load capacity is also 2,000 lb regardless of the number of anchors.
Single anchor fails from concrete edge breakout at 2,000 lb.
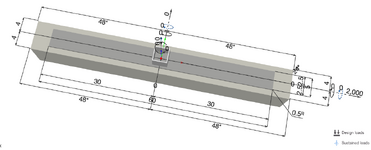
3-anchor group fails from concrete edge breakout at 2,000 lb.
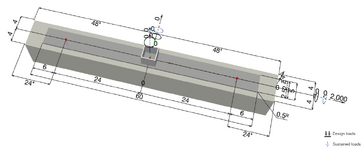
5-anchor group fails from concrete edge breakout at 2,000 lb.
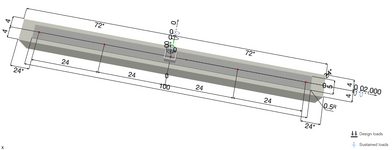
I’m not sure of the right way to interpret this information. For instance, if you had a single angle and single plate using this attachment, you’d develop the 2,000 lb reaction. If 2 ft away, you had another anchor on a separate plate, I believe you’d achieve another 2,000 lb reaction. However, when you put these anchors on the same plate, you get limited to a single breakout capacity based on a single anchor (regardless of the number of anchors). This is due to the limiting geometry perpendicular to the edge, all described through Avc and Avco per ACI 17.7.2.
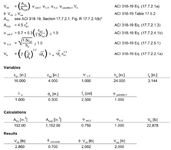
So, what is the right answer? Do I base my numbers of the single anchor, and determine the required field spacing? Limiting multiples groups of anchors to a single anchor's concrete edge breakout seems too conservative.
The reason why I even attempted to put these anchors on the same plate was to make sure their proximity to each other didn’t have some sort of influence.
Let’s say you have a load that is being dragged along a concrete beam and you’re providing post installed anchors to resolve that loading. In this scenario the beam is an 8”x24” concrete beam, and the anchors are provided along the centerline of the 8” dimension (top of beam).
The governing load failure for a single anchor in shear (parallel to length of beam) ends up being concrete edge breakout. This can achieve a strength design reaction of 2,000 lb.
Per Hilti Profis analysis, when providing groups of anchors loaded in the same scenario, the load capacity is also 2,000 lb regardless of the number of anchors.
Single anchor fails from concrete edge breakout at 2,000 lb.
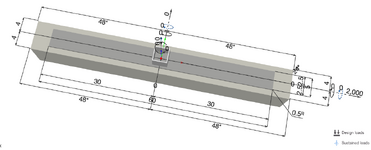
3-anchor group fails from concrete edge breakout at 2,000 lb.
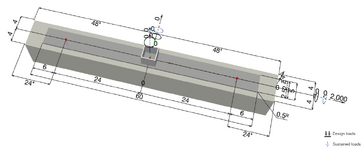
5-anchor group fails from concrete edge breakout at 2,000 lb.
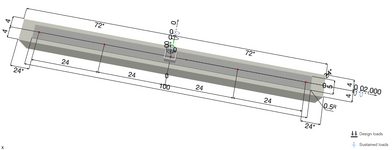
I’m not sure of the right way to interpret this information. For instance, if you had a single angle and single plate using this attachment, you’d develop the 2,000 lb reaction. If 2 ft away, you had another anchor on a separate plate, I believe you’d achieve another 2,000 lb reaction. However, when you put these anchors on the same plate, you get limited to a single breakout capacity based on a single anchor (regardless of the number of anchors). This is due to the limiting geometry perpendicular to the edge, all described through Avc and Avco per ACI 17.7.2.
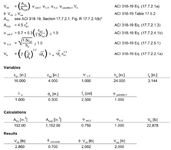
So, what is the right answer? Do I base my numbers of the single anchor, and determine the required field spacing? Limiting multiples groups of anchors to a single anchor's concrete edge breakout seems too conservative.
The reason why I even attempted to put these anchors on the same plate was to make sure their proximity to each other didn’t have some sort of influence.