I am designing a new concrete nib that will sit on an existing suspended slab or beams, 150mm high, 90mm wide. The nib is a retrofit for waterproofing and durability of the non load bearing exterior walls to sit on. There is roughly 600m of nibs to be constructed throughout the 3 storey building. The structural design of it is straight forward with threaded or reinforced bars being epoxy anchored into the existing slab and tied to a straight bar that runs along the nib for shrinkage and crack control. Sometimes the nibs will stop and start between RC columns, sometimes they will be a continuous length up to 20-30m. The nib will be coated in an epoxy membrane to prevent moisture ingress.
The architect has nominated a grout, however they are saying if a concrete could be used there would be a huge saving.
My question is could this be constructed from concrete that is a fine aggregate, flowable concrete mix - say 30-40MPa, or should we be using a low shrinkage high strength grout?
The issues I see with concrete are shrinkage and adhesion to the existing structure, but i'm not sure if it will cause any problems as it is reinforced and has a membrane over it. Scabbling of the existing slab wont be done as the loads are very small.
The architect has nominated a grout, however they are saying if a concrete could be used there would be a huge saving.
My question is could this be constructed from concrete that is a fine aggregate, flowable concrete mix - say 30-40MPa, or should we be using a low shrinkage high strength grout?
The issues I see with concrete are shrinkage and adhesion to the existing structure, but i'm not sure if it will cause any problems as it is reinforced and has a membrane over it. Scabbling of the existing slab wont be done as the loads are very small.
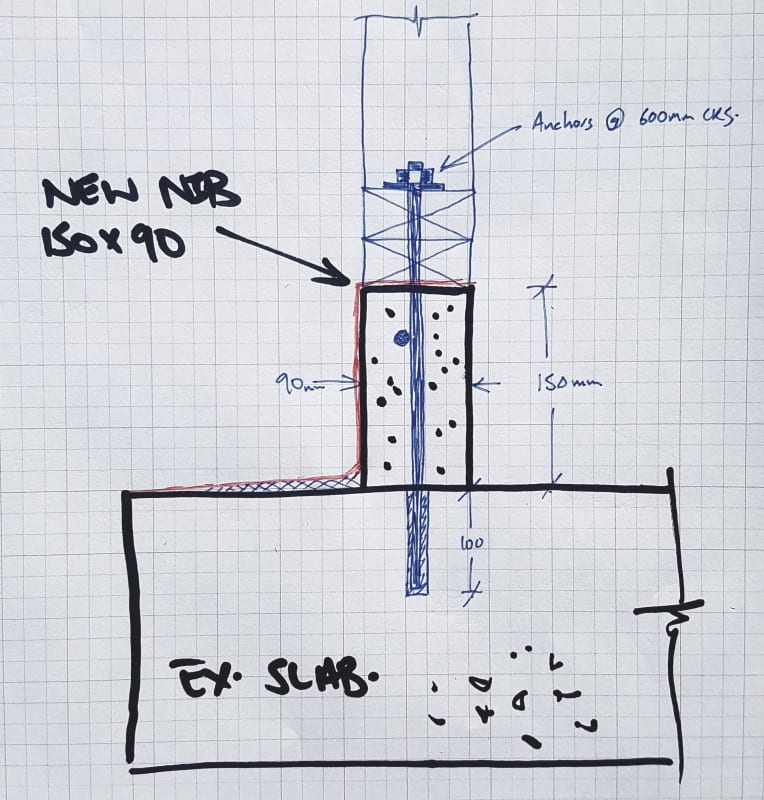