CovertShear
Structural
Let me get right to it:
Problem:
- You have a elevation jump in a monolithic concrete slab (ceiling), or a Z-shape section if you will.
- You want to detail a reinforcement for hogging bending moments M1 and M2 (perpendicular to the "jump beam").
1) I have done this detail before using two outward facing U-shape bends usually.
Question:
- What do you think about the rebar "b1" in the picture?
- I haven't used this yet, but it kinda makes sense to me, the rebar could have a space for development length inside the "jump beam" it seems.
- Basically I want to reinforce the hogging moments M1 and M2 with a single rebar bend, would that work?
Problem:
- You have a elevation jump in a monolithic concrete slab (ceiling), or a Z-shape section if you will.
- You want to detail a reinforcement for hogging bending moments M1 and M2 (perpendicular to the "jump beam").
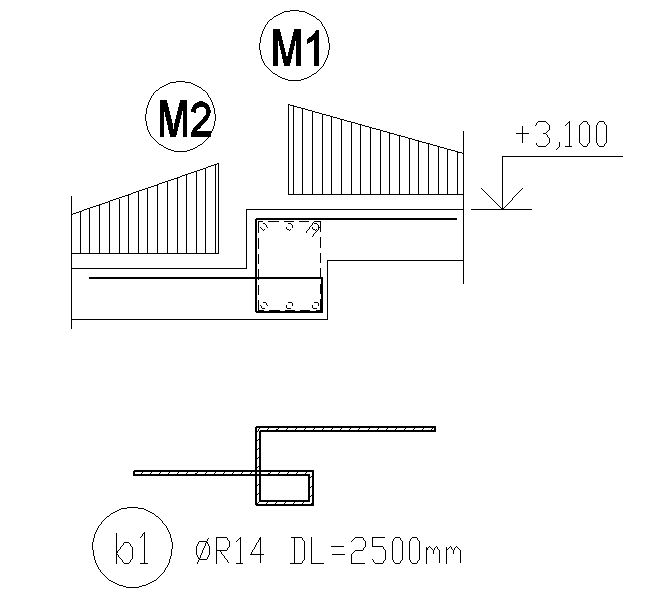
1) I have done this detail before using two outward facing U-shape bends usually.
Question:
- What do you think about the rebar "b1" in the picture?
- I haven't used this yet, but it kinda makes sense to me, the rebar could have a space for development length inside the "jump beam" it seems.
- Basically I want to reinforce the hogging moments M1 and M2 with a single rebar bend, would that work?