Aleeeex
Civil/Environmental
- Aug 14, 2020
- 42
Hi guys,
I am just learning a new software and I came across some new terminology I am not sure about like Axial load release top, and torsional load release top and bottom.
I don't understand what axial load release means? the axial force doesn't go through the column like there is compressible material between the column and the bottom flange of the beam so the beam forces don't go to the ground through the column.
Similarly to torsional load release.
If there is a real connection example with picture with a simple explanation.
Please bare with me!
Thanks
I am just learning a new software and I came across some new terminology I am not sure about like Axial load release top, and torsional load release top and bottom.
I don't understand what axial load release means? the axial force doesn't go through the column like there is compressible material between the column and the bottom flange of the beam so the beam forces don't go to the ground through the column.
Similarly to torsional load release.
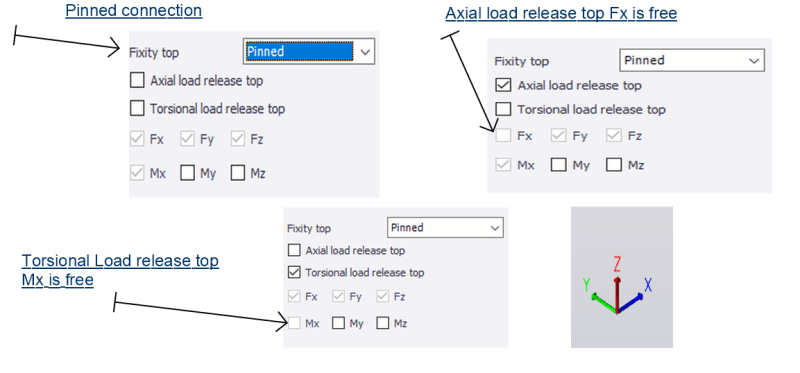
If there is a real connection example with picture with a simple explanation.
Please bare with me!
Thanks