Guys,
I'm evaluating a 60" steam pipe according to ASME Section VIII Div. 2 using Inventor Nastran. There are some branches from 8" to 56" as you can see below; these branches continue as secondary pipes. This pipeline will operate between 170~400ºC (445~675K). I also separated FEA models in three groups(represented by red squares) to simplify load inputs, match with my beam element piping stress analysis software (TRIFLEX) and otimize mesh generation and computational resources.
Taking the mid-piece as example, I created four central points in order to use with Connectors and input displacements/loads given by TRIFLEX analysis.
The most logical way to input these loads, for me, is by applying displacements at points 1/4 associated with Rigid Connector Elements (RBE2) and forces/moments at points 2/3 associated with 'Interpolation' Connector Elements (RBE3). These connectors link central points to correspondent circular edges. But at this point doubts begin:
1 - Every time I consider body temperature and displacements at both 1/4 points, it seems like if the model expands more/less than the difference between displacements of points 1/4. Should there be any difference between beam/3D models expansion between these points? Is usual to consider back extremity (point 4) without any constraints?
2 - Is really necessary to input displacements? I ask because the entire body will expand independently of which displacement is inputted at point 1. It makes sense if studying the effect of friction on stresses around pipe support, for example, but thinking about branches it seems like something that will just complicate my analysis. Forces/moments given by TRIFLEX already consider thermal effects (but separate it between thermal and weight+pressure still possible).
3 - Connectors' DOF. If I consider all translation DOF constrained, relative body expansion on radial directions due to internal pressure and thermal effects are impossible. But allowing these movements, usually calculation returns fatal error due to excessive lack of constraints. I know there is not a 'standard recipe' to do this, but I really don't find trusted content and opinions about, especially talking about Inventor.
Maybe this problem is a little different from usual vessel analysis, but I think that anyone who knows the minimum about how to input loads in nozzles could give me a good orientation.
I would like to say that I'm a beginner with FEA and my knowledge with Inventor Nastran / ASME VIII is limited, so all your opinions and help are always very welcome.
Thanks in advance
Vinício.
I'm evaluating a 60" steam pipe according to ASME Section VIII Div. 2 using Inventor Nastran. There are some branches from 8" to 56" as you can see below; these branches continue as secondary pipes. This pipeline will operate between 170~400ºC (445~675K). I also separated FEA models in three groups(represented by red squares) to simplify load inputs, match with my beam element piping stress analysis software (TRIFLEX) and otimize mesh generation and computational resources.
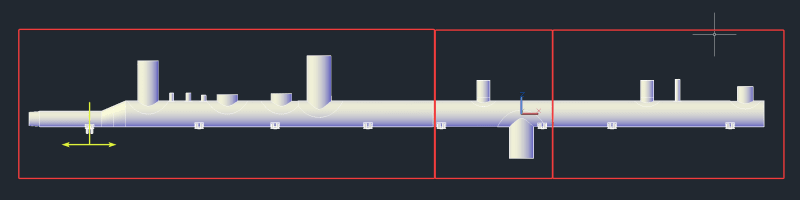
Taking the mid-piece as example, I created four central points in order to use with Connectors and input displacements/loads given by TRIFLEX analysis.
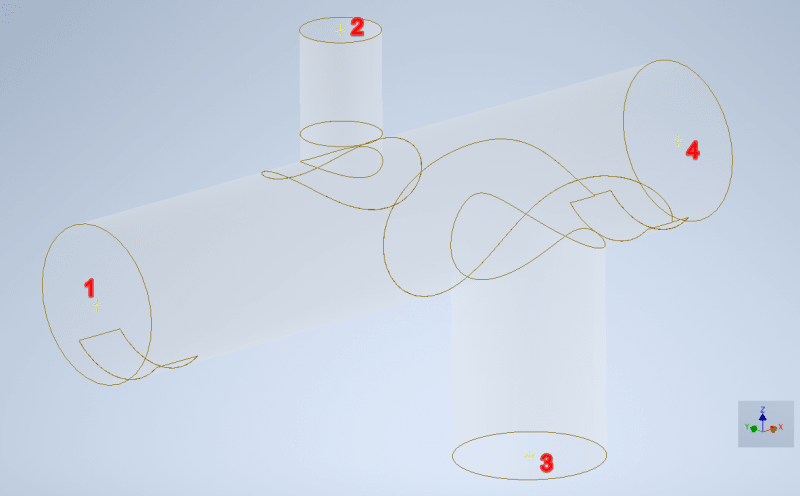
The most logical way to input these loads, for me, is by applying displacements at points 1/4 associated with Rigid Connector Elements (RBE2) and forces/moments at points 2/3 associated with 'Interpolation' Connector Elements (RBE3). These connectors link central points to correspondent circular edges. But at this point doubts begin:
1 - Every time I consider body temperature and displacements at both 1/4 points, it seems like if the model expands more/less than the difference between displacements of points 1/4. Should there be any difference between beam/3D models expansion between these points? Is usual to consider back extremity (point 4) without any constraints?
2 - Is really necessary to input displacements? I ask because the entire body will expand independently of which displacement is inputted at point 1. It makes sense if studying the effect of friction on stresses around pipe support, for example, but thinking about branches it seems like something that will just complicate my analysis. Forces/moments given by TRIFLEX already consider thermal effects (but separate it between thermal and weight+pressure still possible).
3 - Connectors' DOF. If I consider all translation DOF constrained, relative body expansion on radial directions due to internal pressure and thermal effects are impossible. But allowing these movements, usually calculation returns fatal error due to excessive lack of constraints. I know there is not a 'standard recipe' to do this, but I really don't find trusted content and opinions about, especially talking about Inventor.
Maybe this problem is a little different from usual vessel analysis, but I think that anyone who knows the minimum about how to input loads in nozzles could give me a good orientation.
I would like to say that I'm a beginner with FEA and my knowledge with Inventor Nastran / ASME VIII is limited, so all your opinions and help are always very welcome.
Thanks in advance
Vinício.