Hi all
I am modelling neuropathic foot bones. I have segmented 19 bones via MIMICS software. For meshing I used MATIC and Hypermesh. Now I am trying to simulate the neutral standing position of foot with Abaqus/Implicit (Quasi Static).I considered bones to be elastic and giving material (Young's Modulus=7300, poisson's ratio=0.3, density=4.49e-10) to each bone.I fixed the upper surface of tibia and giving concentrated force of 350N from below the ground.
I want to have a surface to surface contact between bones (finite sliding, frictionless) and between foot and ground (hard contact,finite sliding,penalty 0.6) but due to convergence error job get aborted.I tried changing increment in step and through solver control but still getting increment errors.In warnings I am getting some unconnected regions but as its a neuropathic foot it have some bones eroded. I am stuck in this for several days and can't figure out problem in my project. Kindly can someone guide me what I am doing wrong.
Below are some pics of model and warnings.
I am modelling neuropathic foot bones. I have segmented 19 bones via MIMICS software. For meshing I used MATIC and Hypermesh. Now I am trying to simulate the neutral standing position of foot with Abaqus/Implicit (Quasi Static).I considered bones to be elastic and giving material (Young's Modulus=7300, poisson's ratio=0.3, density=4.49e-10) to each bone.I fixed the upper surface of tibia and giving concentrated force of 350N from below the ground.
I want to have a surface to surface contact between bones (finite sliding, frictionless) and between foot and ground (hard contact,finite sliding,penalty 0.6) but due to convergence error job get aborted.I tried changing increment in step and through solver control but still getting increment errors.In warnings I am getting some unconnected regions but as its a neuropathic foot it have some bones eroded. I am stuck in this for several days and can't figure out problem in my project. Kindly can someone guide me what I am doing wrong.
Below are some pics of model and warnings.
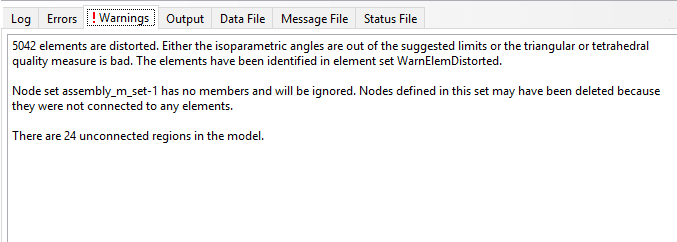
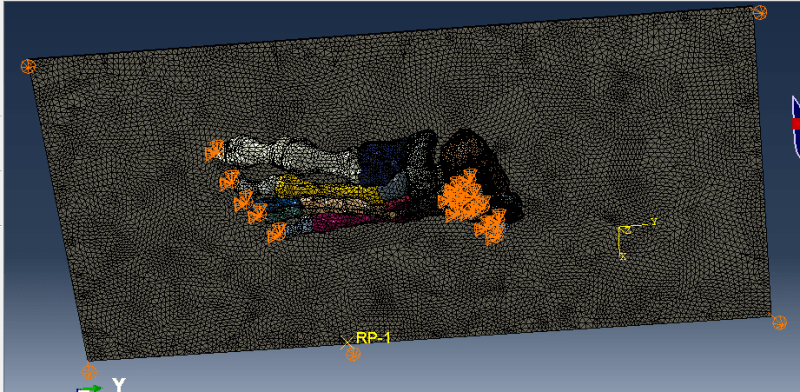
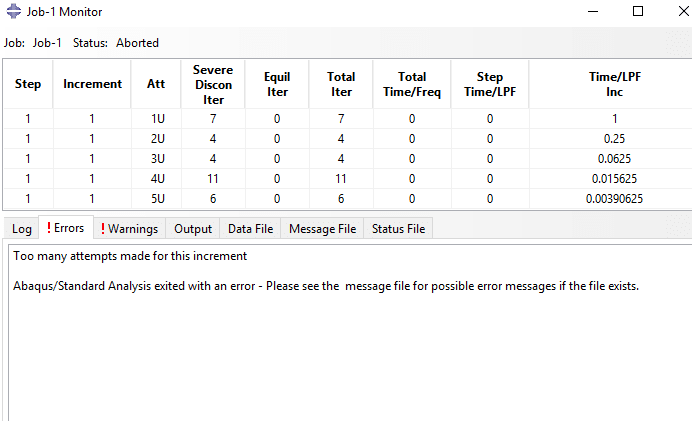