crazyjpeters
Mechanical
So, I'm in the midst of evaluating / modifying our CBD tanks, which were really never evaluated when they switched from AVT(R) to AVT(O). In searching for a maximum nozzle velocity, what I've come to notice is that "Blowdown tanks" CBD or IBD, and any design resources/guides seem to show them being around 1:1 diameter : height. However, steam separators (NZ has produced substantial research and design guides) seem to be 1:3 in diameter : height.
The msx steam inlet velocity appears to be fairly pretty accepted as 40 m/s based on research that Bangma did in 1961, and the designs for these TOC (top-of-cyclone) and BOC (bottom-of-cyclone)separators looks to be fairly well established?
But I really feel they're doing the same job, so why the major difference in vessel design? What concerns me is that the tiny inlet nozzle on our existing vessel has much higher inlet velocity, which is too high and blowing through the vessel wall, but if i slow it down to the conventional New-Zealand style TOC velocity, I'm afraid I'll be dropping it too low with respect to centrifugal acceleration, which is what is doing the water removal.
Am I missing something here?
The msx steam inlet velocity appears to be fairly pretty accepted as 40 m/s based on research that Bangma did in 1961, and the designs for these TOC (top-of-cyclone) and BOC (bottom-of-cyclone)separators looks to be fairly well established?
But I really feel they're doing the same job, so why the major difference in vessel design? What concerns me is that the tiny inlet nozzle on our existing vessel has much higher inlet velocity, which is too high and blowing through the vessel wall, but if i slow it down to the conventional New-Zealand style TOC velocity, I'm afraid I'll be dropping it too low with respect to centrifugal acceleration, which is what is doing the water removal.
Am I missing something here?
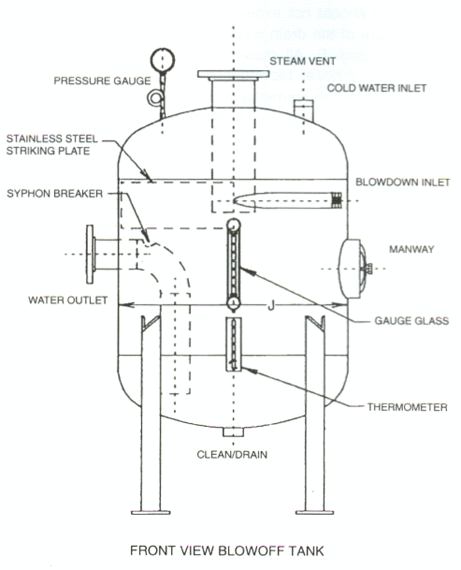
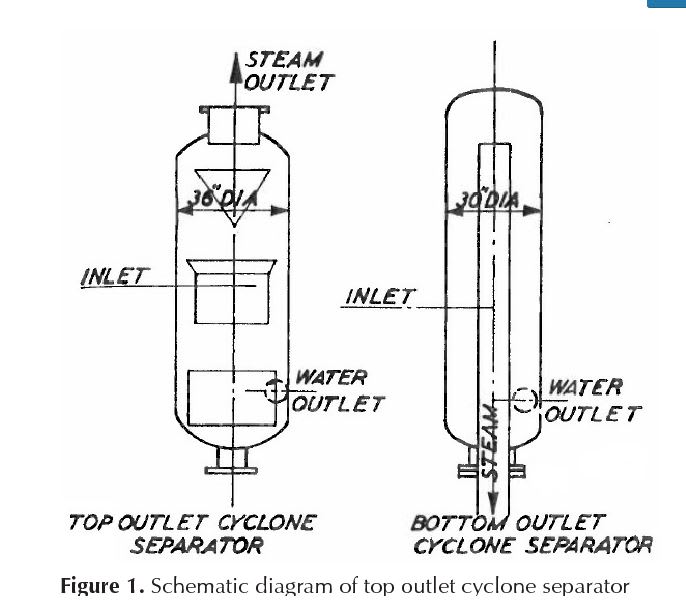