Logan82
Structural
- May 5, 2021
- 212
Hi,
What is the use of a middle rivet in a X bracing? Is it used to reduce the K*L/r ratio? I am asking this because the K*L/r ratio of this bracing is too high (255) if I don't consider the rivet in the middle. I am evaluating this existing structure. It would be odd that the designers at the time (year 1920) would have designed a structure with a K*L/r ratio over 200.
However, I don't see how the middle rivet can really help to support laterally the bracing in compression against buckling perpendicular to the plane of the bracings in X.
What is the use of a middle rivet in a X bracing? Is it used to reduce the K*L/r ratio? I am asking this because the K*L/r ratio of this bracing is too high (255) if I don't consider the rivet in the middle. I am evaluating this existing structure. It would be odd that the designers at the time (year 1920) would have designed a structure with a K*L/r ratio over 200.
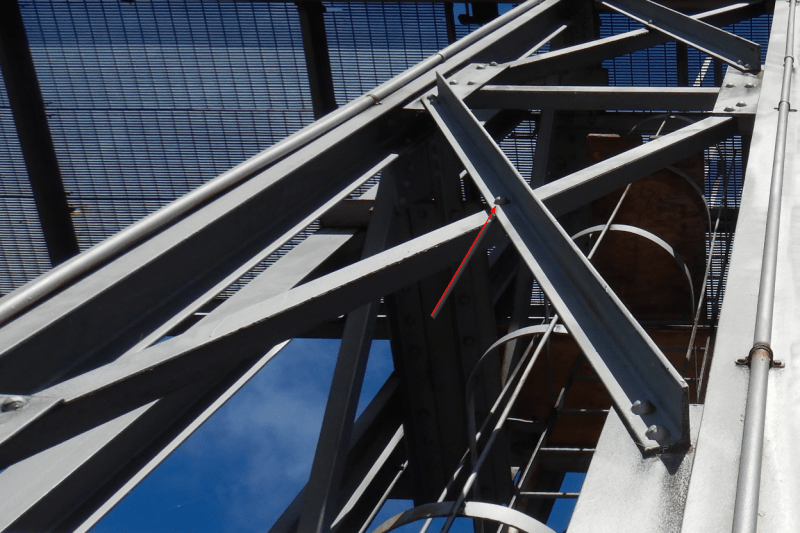
However, I don't see how the middle rivet can really help to support laterally the bracing in compression against buckling perpendicular to the plane of the bracings in X.