Iomcube
Chemical
- Dec 11, 2015
- 187
Our electrolyser produce a constant (fixed) flowrate of 10m3/hr 32%NaOH. Part of this goes to evaporation unit (for producing 50% NaOH) & part of this goes to storage tank.
In the illustration I had added what is to be achieved. First level control of first tank & flow control to evaporation. Per my understanding I will go with this process control scheme. Do please share your input
The second storage tank is a large one. Its pump will run sometimes if the sale of 32% caustic is low & thus evaporation at that time will run at a higher capacity i.e it will take flow both from Electrolyser tank pump & storage pump. Both pumps are identical & the line lengths are no more than 700m
In the illustration I had added what is to be achieved. First level control of first tank & flow control to evaporation. Per my understanding I will go with this process control scheme. Do please share your input
The second storage tank is a large one. Its pump will run sometimes if the sale of 32% caustic is low & thus evaporation at that time will run at a higher capacity i.e it will take flow both from Electrolyser tank pump & storage pump. Both pumps are identical & the line lengths are no more than 700m
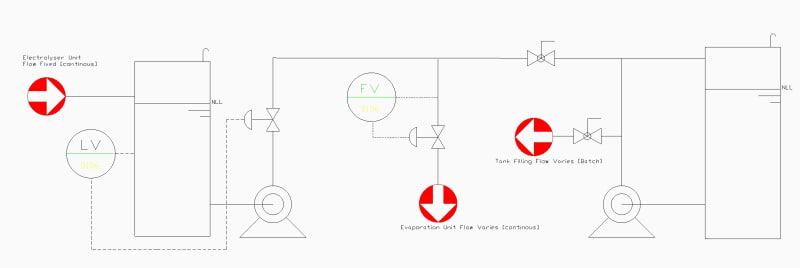