kingkiller
Industrial
Hi, everybody. Figured I'd come over here for some advice on how to proceed with a project I'm working.
First, I'll start by explaining the situation.
I run a music rehearsal facility in Brooklyn, NY called King Killer Studios. We have a garage on the ground floor, but all of our rehearsal rooms are on the second, and we have a funicular lift that is used for hauling equipment (amps, drums, etc.) up to the 2nd level.
The lift is pretty basic: a 3-phase motor couples to a winch system, which either pulls or releases a rope attached to a platform, depending on the direction it's running. There is a 3-button controller (UP [normally open], DOWN [normally open], and STOP [normally closed]) connected to the contactor points of the current relay, as well as two auto-stop switches at the bottom and top of the lift platform, also connected to the contactor points.
Recently, we have had issues with the relay, which I suspect are the result of various archs over time damaging the contacts. It's a VERY old system, and the wiring is an absolute rat's nest and needs to be cleaned up no matter what I decide to do. The biggest issue is that occasionally, the "auto stop" switches (both normally closed, like the STOP button) have been failing at the top, leading the platter to slam against the top platform, which in turn makes the chain slip and eventually break. When that happens, well...I'm sure you can figure that out. With no tension keeping the winch in place, the platter flies down the lift riser (about 35 feet), and slams into the bottom. If someone were standing there, it would be bad news, obviously.
SO:
The "auto stop" switches are brand new. I tested them for continuity before installing, and again after the latest incident, and they have a 0% failure rate. The motor was recently respun, and is working fine. I have also tested the controller box, and each of the momentary switches seems to be working correctly (however, the few times that this has happened, pressing the STOP button did nothing), which leads me to believe the electromechanical relay is worn out and beginning to fail more often, which I can't have.
I've decided to replace it, and I've purchased a 3-phase reversing relay from Mouser (the Crydom D53RV25C). However, I have a few questions.
1) The motor is pretty old, and I'm unsure how many HP it is. The main fuse/cutoff box says it is RATED for 7.5 HP, but I do not think the motor is that big. We have 3 legs of 120V/20A coming into the box, on which the motor runs solidly, which is why I purchased the 25C instead of the 50C; it is rated for up to 25A PER PHASE, which is already higher than the motor is running on. Should I have gotten the larger one (rated at 50A/phase), and why?
2) I am confused about the contactor connections. There are two terminals, one for forward, and one for reverse, and one common terminal for both, which makes sense. However, it seems as though the contactor itself needs to be powered separately, with a range of 4-32V. Will I be able to retrofit my existing switchbox and auto stop switches, or will I need to revamp the entire contactor/control system? If I can use what I currently have, how would I go about it? There is very little data on this specific SSR, and I'm unsure whether or not it supplies the control voltage, though it seems as though it does not.
3) VARISTORS. The SSR I purchased has only 2 legs that get reversed depending on the direction they are told to spin. One datasheet I read recommended attaching MOVs (or VARISTORS) between each "active" phase and it's reverse counterpart, both outside and within the SSR, for a total of 4 (see picture below). For this circuit, what would be the recommended value of this MOV?
4) Will this SSR require a heatsink for this application?
5) Here's the big question: should I just get a new electromechanical relay and rewire the whole system, essentially as is, but get rid of the mess of wires? The wiring will be redone one way or another, but I'm starting to wonder if I should just keep the system as is to keep my costs down.
Please let me know how I should proceed. Time is also of the essence, because I have a large clientele all getting impatient with each passing day that the lift is not working!
Here are some more pics of this whole mess:
First, I'll start by explaining the situation.
I run a music rehearsal facility in Brooklyn, NY called King Killer Studios. We have a garage on the ground floor, but all of our rehearsal rooms are on the second, and we have a funicular lift that is used for hauling equipment (amps, drums, etc.) up to the 2nd level.
The lift is pretty basic: a 3-phase motor couples to a winch system, which either pulls or releases a rope attached to a platform, depending on the direction it's running. There is a 3-button controller (UP [normally open], DOWN [normally open], and STOP [normally closed]) connected to the contactor points of the current relay, as well as two auto-stop switches at the bottom and top of the lift platform, also connected to the contactor points.
Recently, we have had issues with the relay, which I suspect are the result of various archs over time damaging the contacts. It's a VERY old system, and the wiring is an absolute rat's nest and needs to be cleaned up no matter what I decide to do. The biggest issue is that occasionally, the "auto stop" switches (both normally closed, like the STOP button) have been failing at the top, leading the platter to slam against the top platform, which in turn makes the chain slip and eventually break. When that happens, well...I'm sure you can figure that out. With no tension keeping the winch in place, the platter flies down the lift riser (about 35 feet), and slams into the bottom. If someone were standing there, it would be bad news, obviously.
SO:
The "auto stop" switches are brand new. I tested them for continuity before installing, and again after the latest incident, and they have a 0% failure rate. The motor was recently respun, and is working fine. I have also tested the controller box, and each of the momentary switches seems to be working correctly (however, the few times that this has happened, pressing the STOP button did nothing), which leads me to believe the electromechanical relay is worn out and beginning to fail more often, which I can't have.
I've decided to replace it, and I've purchased a 3-phase reversing relay from Mouser (the Crydom D53RV25C). However, I have a few questions.
1) The motor is pretty old, and I'm unsure how many HP it is. The main fuse/cutoff box says it is RATED for 7.5 HP, but I do not think the motor is that big. We have 3 legs of 120V/20A coming into the box, on which the motor runs solidly, which is why I purchased the 25C instead of the 50C; it is rated for up to 25A PER PHASE, which is already higher than the motor is running on. Should I have gotten the larger one (rated at 50A/phase), and why?
2) I am confused about the contactor connections. There are two terminals, one for forward, and one for reverse, and one common terminal for both, which makes sense. However, it seems as though the contactor itself needs to be powered separately, with a range of 4-32V. Will I be able to retrofit my existing switchbox and auto stop switches, or will I need to revamp the entire contactor/control system? If I can use what I currently have, how would I go about it? There is very little data on this specific SSR, and I'm unsure whether or not it supplies the control voltage, though it seems as though it does not.
3) VARISTORS. The SSR I purchased has only 2 legs that get reversed depending on the direction they are told to spin. One datasheet I read recommended attaching MOVs (or VARISTORS) between each "active" phase and it's reverse counterpart, both outside and within the SSR, for a total of 4 (see picture below). For this circuit, what would be the recommended value of this MOV?
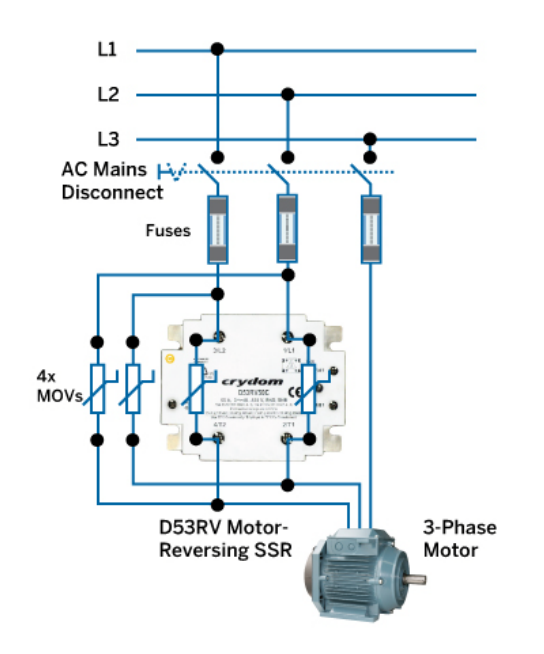
4) Will this SSR require a heatsink for this application?
5) Here's the big question: should I just get a new electromechanical relay and rewire the whole system, essentially as is, but get rid of the mess of wires? The wiring will be redone one way or another, but I'm starting to wonder if I should just keep the system as is to keep my costs down.
Please let me know how I should proceed. Time is also of the essence, because I have a large clientele all getting impatient with each passing day that the lift is not working!
Here are some more pics of this whole mess:
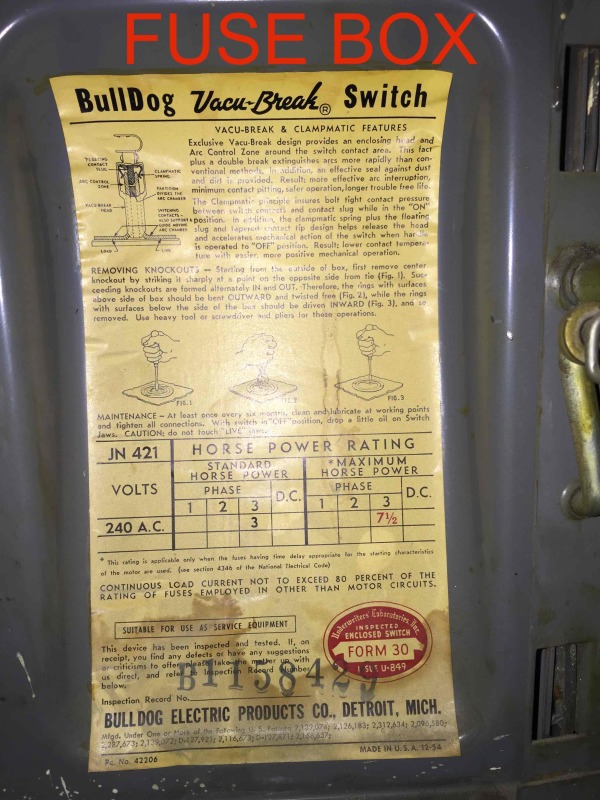
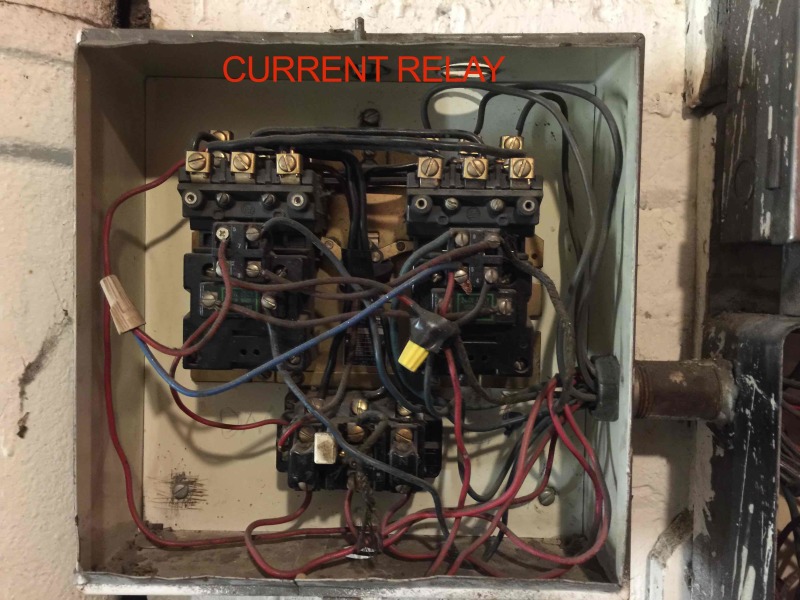
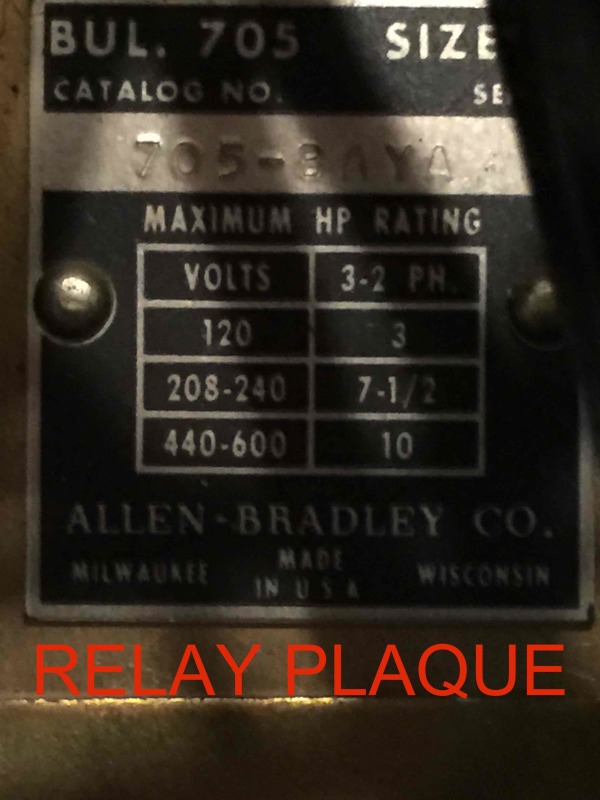
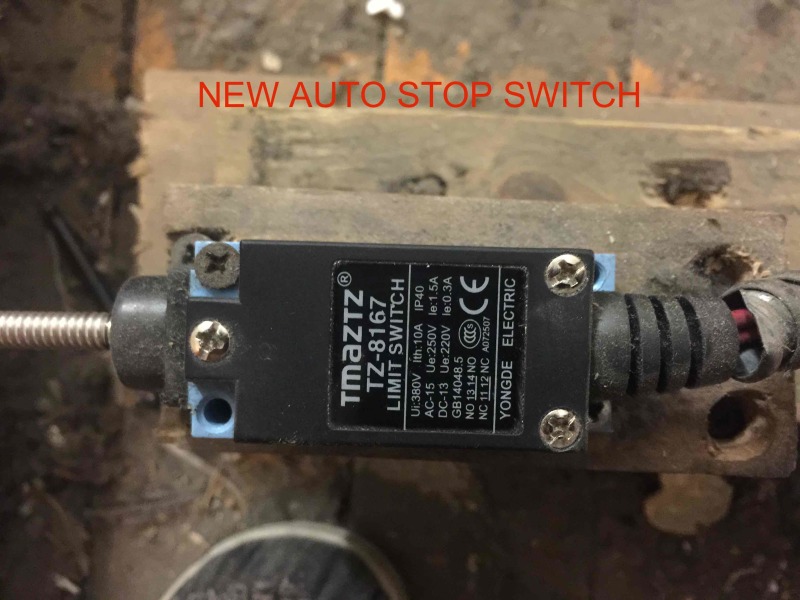
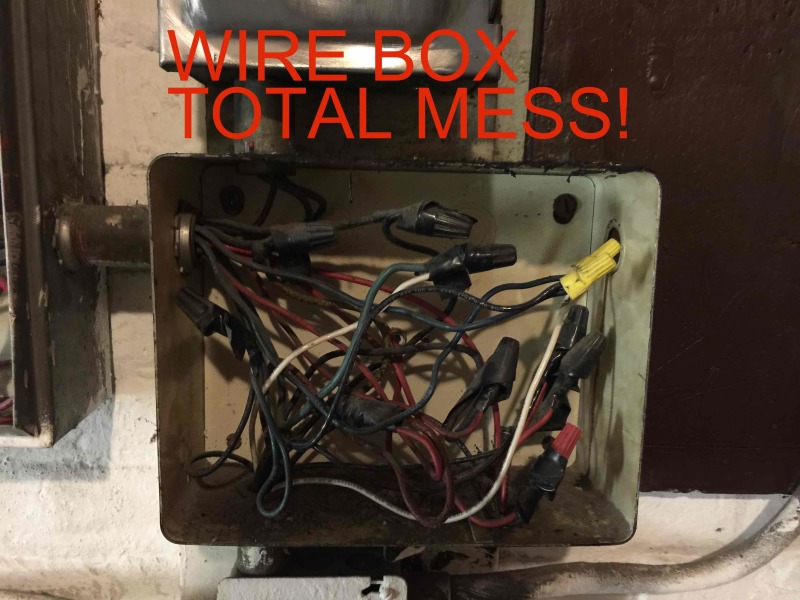