I would like to heat a piece of track work rail steel of the following profile to the following temperature distribution, all shown in the picture at the link.
This track work can be of that cross-section in the link above, but extruded up to 80 feet long and is made of a low-alloy steel with a pearlitic microstructure. I want to keep the pearlite microstructure, but I just want to heat about 3-4 feet in length of the rail extrusion to the temperature distribution shown in the above link. The chemical composition of the steel is shown in the below link.
If I were to heat the base of the rail (where it shows the temperature range to be 1000 to 1600 degrees Fahrenheit) to 1200 degrees Fahrenheit, and the head of the rail (where it shows the temperature range to be 650 to 850 degrees Fahrenheit) to 750 degrees Fahrenheit, how quickly could I bring the steel down to room temperature throughout its entire mass (72 degrees Fahrenheit) in the following quench scenarios while avoiding the formation of martensite in the steel?
1) Completely submerged in 72 degree Fahrenheit, still water.
2) Sitting on concrete at 60 degrees Fahrenheit in still air (observed to take 6-10 hours).
3) Cooled through application of water misting.
4) Sitting in front of a 48" diameter fan which produces 19500 CFM with the airflow running transverse to the length of the rail extrusion.
5) Cooled by direct application of liquid nitrogen (observed to take 12 minutes but unknown if the microstructure was changed).
Any advice in this realm would be much appreciated because I am very lost on this and I don't have any Jominy charts or anything to look at cooling rates or evaluate anything analytically for this specific type of steel.
Please and Thank You
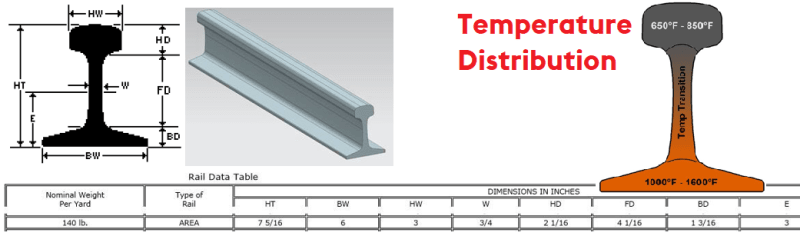
This track work can be of that cross-section in the link above, but extruded up to 80 feet long and is made of a low-alloy steel with a pearlitic microstructure. I want to keep the pearlite microstructure, but I just want to heat about 3-4 feet in length of the rail extrusion to the temperature distribution shown in the above link. The chemical composition of the steel is shown in the below link.
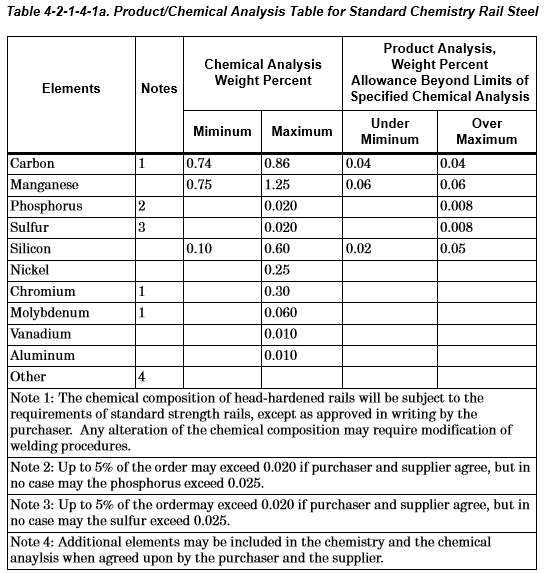
If I were to heat the base of the rail (where it shows the temperature range to be 1000 to 1600 degrees Fahrenheit) to 1200 degrees Fahrenheit, and the head of the rail (where it shows the temperature range to be 650 to 850 degrees Fahrenheit) to 750 degrees Fahrenheit, how quickly could I bring the steel down to room temperature throughout its entire mass (72 degrees Fahrenheit) in the following quench scenarios while avoiding the formation of martensite in the steel?
1) Completely submerged in 72 degree Fahrenheit, still water.
2) Sitting on concrete at 60 degrees Fahrenheit in still air (observed to take 6-10 hours).
3) Cooled through application of water misting.
4) Sitting in front of a 48" diameter fan which produces 19500 CFM with the airflow running transverse to the length of the rail extrusion.
5) Cooled by direct application of liquid nitrogen (observed to take 12 minutes but unknown if the microstructure was changed).
Any advice in this realm would be much appreciated because I am very lost on this and I don't have any Jominy charts or anything to look at cooling rates or evaluate anything analytically for this specific type of steel.
Please and Thank You