Dglock18
Mechanical
- Sep 18, 2015
- 5
Hi,
My company uses a lot of INC 625 superalloy for our fixture equipment in testing SOFC (Solid Oxide Fuel Cells), because of it's well know high temperature corrosion resistance (SOFC's typically operate at around 800C). This metal has been great for the most part, until recently...
Upon disassembling cell stacks, I notice many times that we have heavy pitting and greenish-type corrosion occurring in air at about 800C, and sometimes not for very long at that temp (a few days even). This is especially severe when we use silver mesh (99.9%, 80 mesh) as a means to increase electrical conductivity between the top of a fuel cell stack and the INC 625 plate with a current collecting rod attached.
I have looked all over the internet to learn more about why this is occurring, and to try and mitigate this effect from happening, as this material is VERY expensive to both purchase and then machine into usable fixtures for use in fuel cell testing.
Does anyone have any idea what I could do to reduce or eliminate this type of corrosion?
Thanks, Dglock18
My company uses a lot of INC 625 superalloy for our fixture equipment in testing SOFC (Solid Oxide Fuel Cells), because of it's well know high temperature corrosion resistance (SOFC's typically operate at around 800C). This metal has been great for the most part, until recently...
Upon disassembling cell stacks, I notice many times that we have heavy pitting and greenish-type corrosion occurring in air at about 800C, and sometimes not for very long at that temp (a few days even). This is especially severe when we use silver mesh (99.9%, 80 mesh) as a means to increase electrical conductivity between the top of a fuel cell stack and the INC 625 plate with a current collecting rod attached.
I have looked all over the internet to learn more about why this is occurring, and to try and mitigate this effect from happening, as this material is VERY expensive to both purchase and then machine into usable fixtures for use in fuel cell testing.
Does anyone have any idea what I could do to reduce or eliminate this type of corrosion?
Thanks, Dglock18
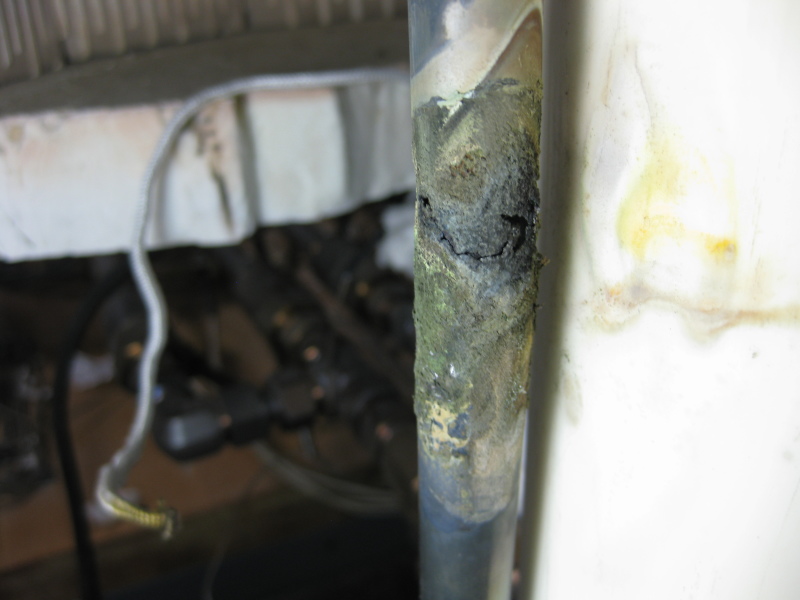
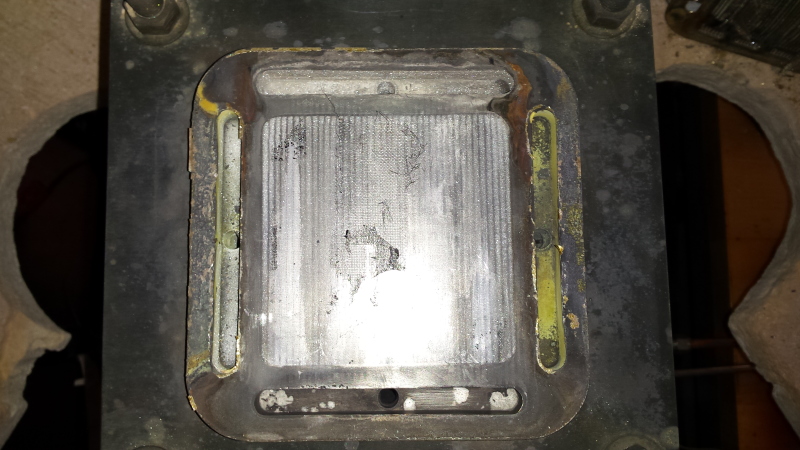