rtiwari123
Mechanical
- Mar 22, 2016
- 8
Hi Al,
Can anyone take a look at the two pictures below and advise the cause for the fracture shown here.
It is an oil separator tank made from SA 455 material. To my knowledge there are no temperature extremes and vibrations in service. Material is 0.25" thick; it is code vessel. Thanks in advance.
Can anyone take a look at the two pictures below and advise the cause for the fracture shown here.
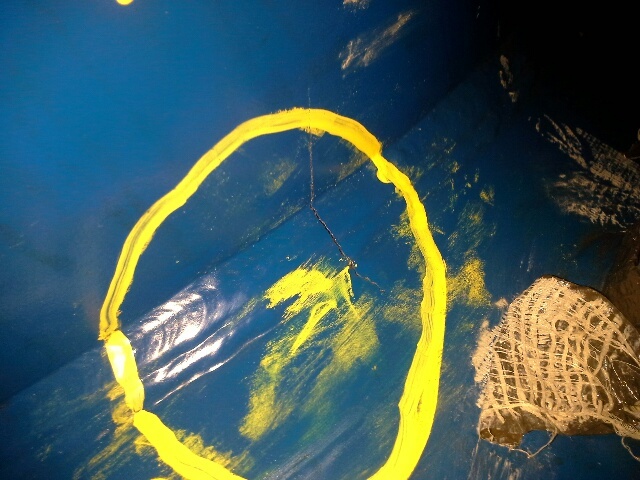
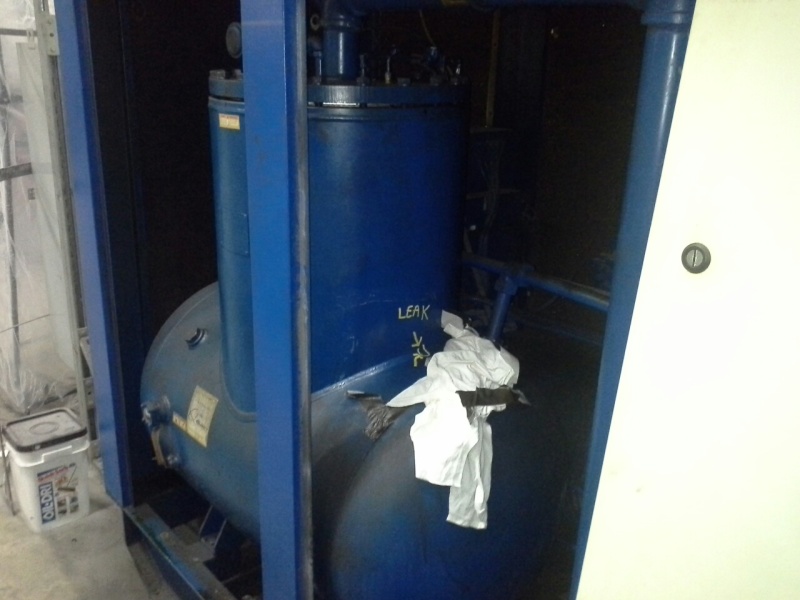
It is an oil separator tank made from SA 455 material. To my knowledge there are no temperature extremes and vibrations in service. Material is 0.25" thick; it is code vessel. Thanks in advance.