SteelPE
Structural
- Mar 9, 2006
- 2,759
I am in the process of putting an addition on an existing industrial building with some interior cranes (circa late 60’s). The building is 3 bays wide and currently has all three bays occupied with cranes. We are going to remove the end wall of the building to put on our addition. We are going to be placing new columns 1’-6” away from the existing building columns. Current code = IBC 2015.
I am a bit uncomfortable with the existing end wall columns…. And actually, most of the columns inside of the existing building. No matter how I run my analysis, I just can’t get the existing columns end wall columns to work (I am guessing this is because of the computer analysis I am doing today vs the way it was designed 50+ years ago). So, after much thinking I have decided that I am going to apply some channels across the tips of the flanges (see attached) and make a box section out of the existing column. Based upon my rough analysis, I can get the columns to work with this reinforcing (full height).
The question revolves around welding of the channels to the columns. Since this loading is going to be cyclical (due to the cranes) should this weld be continuous or could it be intermittent (stitch welded on)?
I am a bit uncomfortable with the existing end wall columns…. And actually, most of the columns inside of the existing building. No matter how I run my analysis, I just can’t get the existing columns end wall columns to work (I am guessing this is because of the computer analysis I am doing today vs the way it was designed 50+ years ago). So, after much thinking I have decided that I am going to apply some channels across the tips of the flanges (see attached) and make a box section out of the existing column. Based upon my rough analysis, I can get the columns to work with this reinforcing (full height).
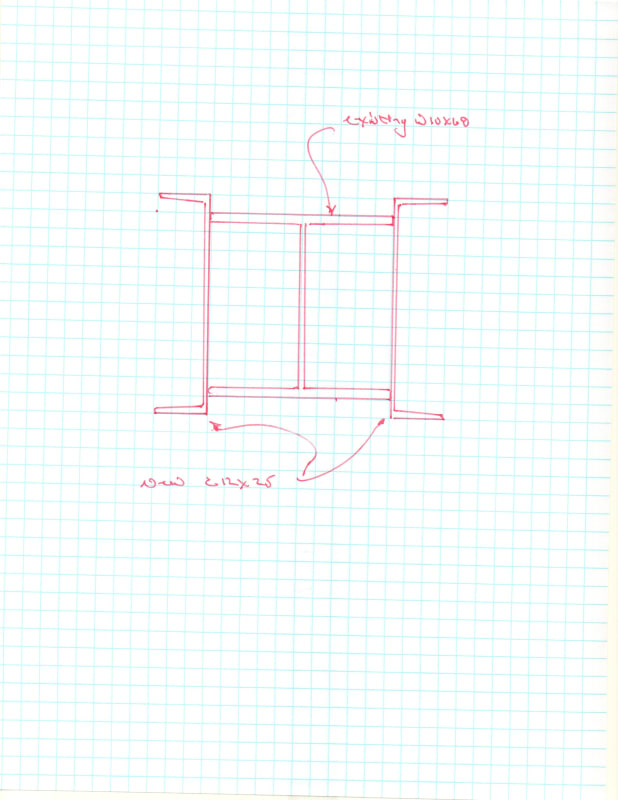
The question revolves around welding of the channels to the columns. Since this loading is going to be cyclical (due to the cranes) should this weld be continuous or could it be intermittent (stitch welded on)?