Deividas
Automotive
- Dec 14, 2014
- 106
Hi everyone! I have some questions about crankcase vent systems with pcv valves.
there is one system
there is another system
and there is pcv valve
My question is, when and how fresh air from intake before throttle plate could flow INTO crankcase? Like in second picture. If at idle pcv highly restricts air coming from crankcase, then pressure in crankcase should be less than atmospheric to draw air from intake before throttle plate via breather tube.
If engine running at WOT, then pcv also closes, because pressure after throttle plate is about atmospheric and all blow-by gases should go out via breather tube, which is before throttle plate, but only if crankcase has higher pressure than atmospheric. (Or via pcv, if crankcase pressure eovercome pcv spring force).
So pcv is open only at mid engine load (like in 3rd pic) and then in crankcase maybe is slightly vacuum, and in that situation can be, that air comes IN crankcase from breather tube which is before throttle plate (like in 2nd pic)? OR all system should work like in first picture, when fresh air never comes into crankcase? Or maybe i don't understand something?
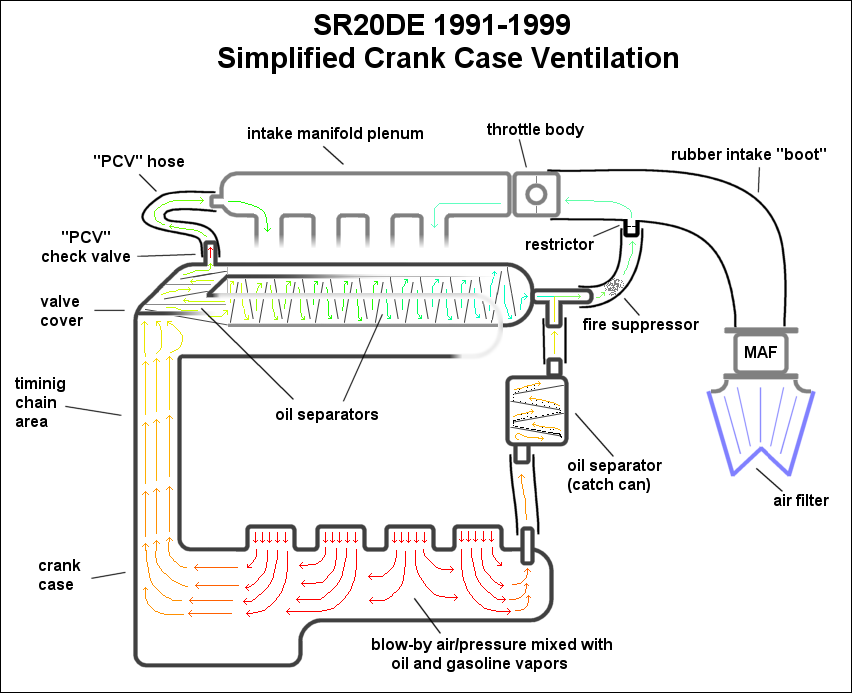
there is one system

there is another system
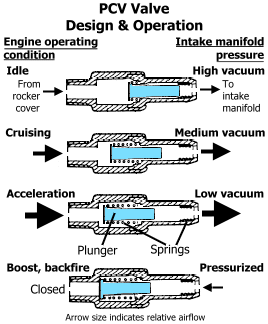
and there is pcv valve
My question is, when and how fresh air from intake before throttle plate could flow INTO crankcase? Like in second picture. If at idle pcv highly restricts air coming from crankcase, then pressure in crankcase should be less than atmospheric to draw air from intake before throttle plate via breather tube.
If engine running at WOT, then pcv also closes, because pressure after throttle plate is about atmospheric and all blow-by gases should go out via breather tube, which is before throttle plate, but only if crankcase has higher pressure than atmospheric. (Or via pcv, if crankcase pressure eovercome pcv spring force).
So pcv is open only at mid engine load (like in 3rd pic) and then in crankcase maybe is slightly vacuum, and in that situation can be, that air comes IN crankcase from breather tube which is before throttle plate (like in 2nd pic)? OR all system should work like in first picture, when fresh air never comes into crankcase? Or maybe i don't understand something?