Hi all,
At first it seemed like an easy thing to do, but not so sure now
.
I need to assemble a Hub on a D-shaft of 15mm Dia., the Hub already has a hole of 10mm Dia. so it needs to be enlarged and create the "shelf".
.
Can this be done without creating large radius (anything over R1 mm) at the seem between the hole and the "shelf"?
At first it seemed like an easy thing to do, but not so sure now
![[ponder] [ponder] [ponder]](/data/assets/smilies/ponder.gif)
I need to assemble a Hub on a D-shaft of 15mm Dia., the Hub already has a hole of 10mm Dia. so it needs to be enlarged and create the "shelf".
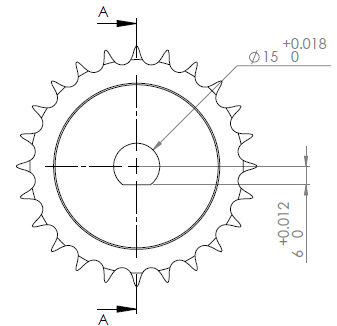
Can this be done without creating large radius (anything over R1 mm) at the seem between the hole and the "shelf"?