yaroosh
Structural
- May 11, 2015
- 32
Hello Everyone,
Again I am asking about creep and shrinkage. I have been doing some research to be able to understand why as time progresses, my moment demand increases tremendously.
I am working on the widening of a 4 span precast prestressed bridge with cast in place Deck.
I am using CSI Bridge where I defined my concrete properties to be time dependent materials
I ran a stage analysis as follow
-Stage 1: Existing
-Stage 2:time lapse
-Stage 3: Abutments
-Stage 4: piles and Girders
-Stage 5: prestress
-Stage 6: 7 days for creep and shrinkage
-stage 7-1: Haunch
-Stage 7-2: Wet Deck
-Stage 7-3
eck Harden
-stage 7-4: Creep and Shrinkage (7days)
-Stage 8: permanent loads
-Stage 10: creep and shrinkage (18250 days)
This is stage 6 results
This is Stage 7-4
I apologize for the long post. But if someone can shed some light, it will help me greatly!
Thanks!
Again I am asking about creep and shrinkage. I have been doing some research to be able to understand why as time progresses, my moment demand increases tremendously.
I am working on the widening of a 4 span precast prestressed bridge with cast in place Deck.
I am using CSI Bridge where I defined my concrete properties to be time dependent materials
I ran a stage analysis as follow
-Stage 1: Existing
-Stage 2:time lapse
-Stage 3: Abutments
-Stage 4: piles and Girders
-Stage 5: prestress
-Stage 6: 7 days for creep and shrinkage
-stage 7-1: Haunch
-Stage 7-2: Wet Deck
-Stage 7-3
-stage 7-4: Creep and Shrinkage (7days)
-Stage 8: permanent loads
-Stage 10: creep and shrinkage (18250 days)
This is stage 6 results
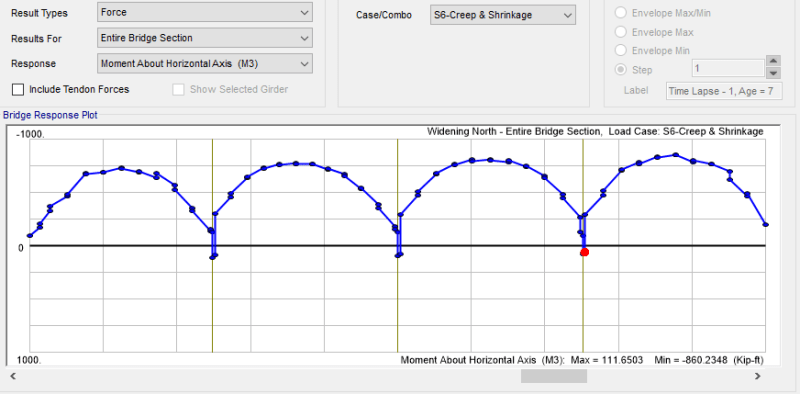
This is Stage 7-4
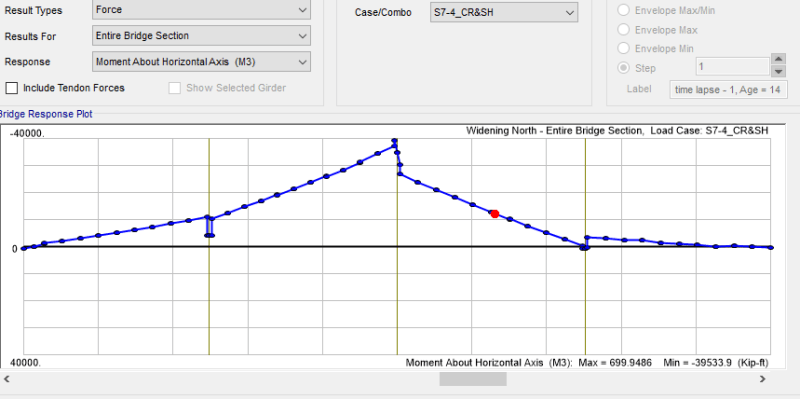
I apologize for the long post. But if someone can shed some light, it will help me greatly!
Thanks!