struct_eeyore
Structural
I've got condition where I need to support an existing 3-ply 2x8 beam on both sides with hangers - however, the hangers must be spaced such that they can attach to beam clips on an existing WF beam up above, requiring several plies of blocking. (see attached image) The loads overall are not large - the hanger attaching directly to the beam will be about 260lb, while the one at the blocking will be 175lb; however, my concern is that this multi ply condition now acts as it's own beam perpendicular to the span of the existing 3-ply. Assuming a 5" wide strip (about 3x the width of the hanger connector) results in a cross grain tension stress of about 13psi, which is about in line with the info from APA if I remember correctly. I'm now left to debate if this approach is allowable by code, and even if so, if it's appropriate.
Note - this is 0 wind, live, or seismic application - inaccessible suspended ceiling with heavy wood framing.
Thanks in advance.
at the bottom with a 20ga strap
Note - this is 0 wind, live, or seismic application - inaccessible suspended ceiling with heavy wood framing.
Thanks in advance.
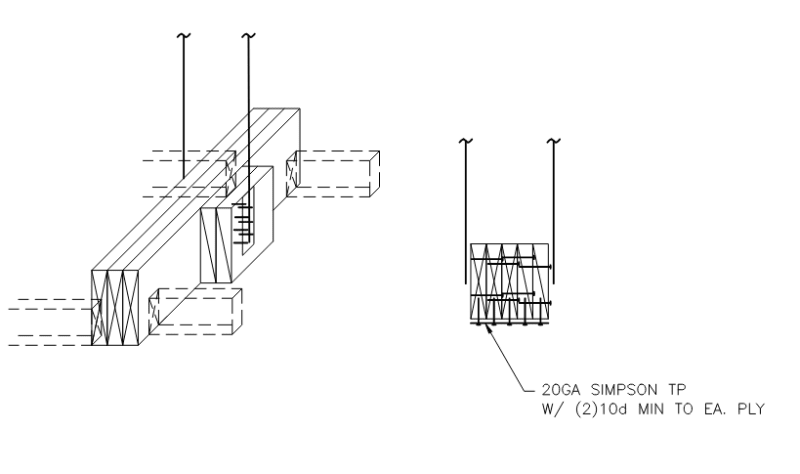