-
1
- #1
bhiggins
Structural
- Oct 15, 2016
- 152
Hello engineers!
I have a very unique project. A client wants to design a $200k+ curved steel staircase. The intent is to have the stringer "carved" by the steps and have a minimal "effective" depth of stringer. I modeled it in RISA3D with 1/4" thick threads and risers, and 1/2" thick stringer plate elements. The model seems to be working too good. I've tried it with an "effective" stringer depth of 4" and the deflections throughout are less than 1/4". It appears that the curved shape is helping substantially, though the reactions are quite high. My aim is to keep stresses under 1/3 Fy and deflections under 1/4". The entire stair is loaded to 100 PSF.
I also tried modeling the stringers as stick .5"x 4" rectangular elements tied together with plates and the results have been similar. It appears that the shape is causing deflections to be at minimum.
I am wondering if anyone has experience designing anything similar in the past. My intuition says to go much deeper with the stringers (around 8"), but the depth hasn't been affecting deflections much due to the entire structure being strong as one unit. If anyone else has useful advice it would be much appreciated!
I have a very unique project. A client wants to design a $200k+ curved steel staircase. The intent is to have the stringer "carved" by the steps and have a minimal "effective" depth of stringer. I modeled it in RISA3D with 1/4" thick threads and risers, and 1/2" thick stringer plate elements. The model seems to be working too good. I've tried it with an "effective" stringer depth of 4" and the deflections throughout are less than 1/4". It appears that the curved shape is helping substantially, though the reactions are quite high. My aim is to keep stresses under 1/3 Fy and deflections under 1/4". The entire stair is loaded to 100 PSF.
I also tried modeling the stringers as stick .5"x 4" rectangular elements tied together with plates and the results have been similar. It appears that the shape is causing deflections to be at minimum.
I am wondering if anyone has experience designing anything similar in the past. My intuition says to go much deeper with the stringers (around 8"), but the depth hasn't been affecting deflections much due to the entire structure being strong as one unit. If anyone else has useful advice it would be much appreciated!
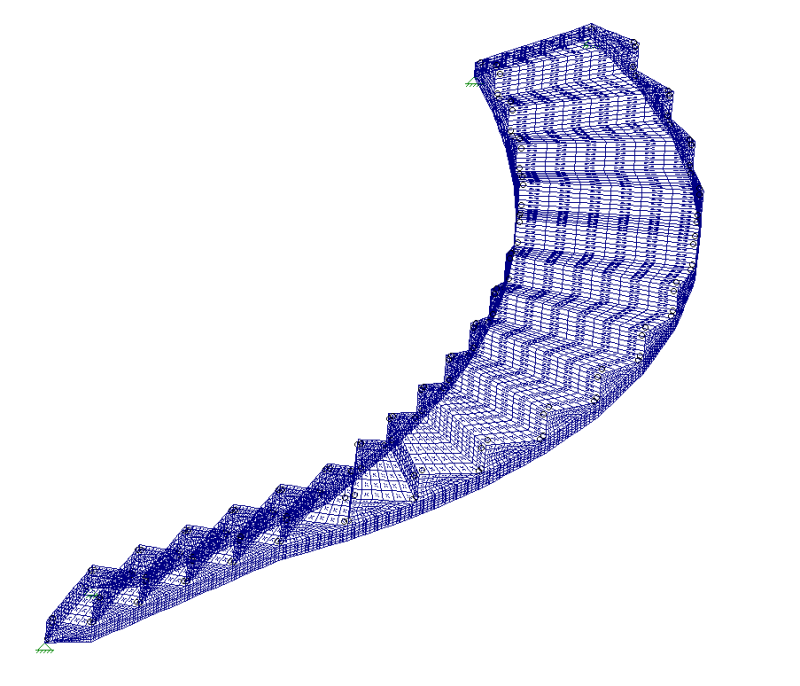