Hi,
I have a question regarding a custom spot welding application: Is it possible to spot weld through the thin edge of a sheet metal (~3mm) rib standing perpindicular to a mating flat sheet (~0.5mm)? (See attached pic)
And the sheets may be pre-galvanised!
My experience with RSW is limited so not sure if this idea is technically feasible.
As a follow up question, with this application could the spot weld be ganged, ie n-welds along the rib per cycle?
Thanks, Richard
I have a question regarding a custom spot welding application: Is it possible to spot weld through the thin edge of a sheet metal (~3mm) rib standing perpindicular to a mating flat sheet (~0.5mm)? (See attached pic)
And the sheets may be pre-galvanised!
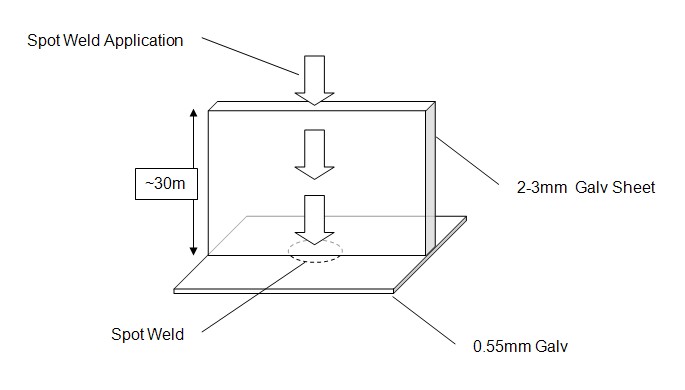
My experience with RSW is limited so not sure if this idea is technically feasible.
As a follow up question, with this application could the spot weld be ganged, ie n-welds along the rib per cycle?
Thanks, Richard