VaggelisKas
Industrial
- May 11, 2015
- 36
Hello community,
I am trying to calculate the stresses during a cutting sequence.
However I can not see the stresses on the tool, only on the workpiece
What I mean is as follows:
What I mean to accomplish is to show the stress contours on the tool as well as the workpiece.
Both the tool and the workpiece are meshed with the same elements (Plane Strain Elements, CPE4R).
Any ideas would be highly appreciated.
I am trying to calculate the stresses during a cutting sequence.
However I can not see the stresses on the tool, only on the workpiece
What I mean is as follows:
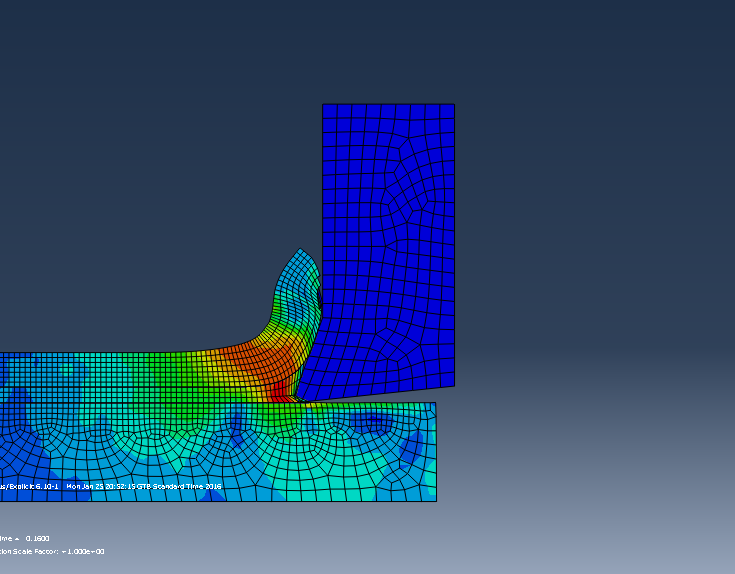
What I mean to accomplish is to show the stress contours on the tool as well as the workpiece.
Both the tool and the workpiece are meshed with the same elements (Plane Strain Elements, CPE4R).
Any ideas would be highly appreciated.