tmalik3156
Structural
Good day all.
We are going to design a cylindrical concrete foundation for a large overhead highway sign structure.
The manufacturer of the sign structure will provide us with the forces and the moments at the top of the foundation. A sample is shown below. Notice the high torsion.
We also have Geotechnical Report where soil skin friction values are provided. A sample is shown below.
The foundation cylinder diameter is not to be over 1.6 m. The final output would look something like this.
We have not done such a design before. If you are familiar with such design, kindly advise us on:
• How to design for torsion
• Comments on practical maximum depth of the cylinder
• Most critical thing to check in the design (What is the weakest link of the chain?)
If you could share design examples / calculations / drawings, that would also be highly appreciated.
We are going to design a cylindrical concrete foundation for a large overhead highway sign structure.
The manufacturer of the sign structure will provide us with the forces and the moments at the top of the foundation. A sample is shown below. Notice the high torsion.
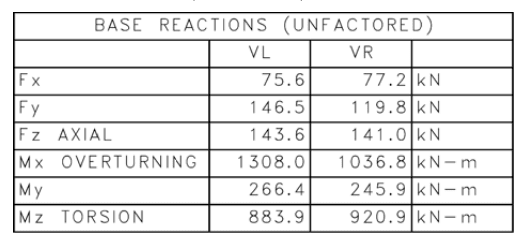
We also have Geotechnical Report where soil skin friction values are provided. A sample is shown below.
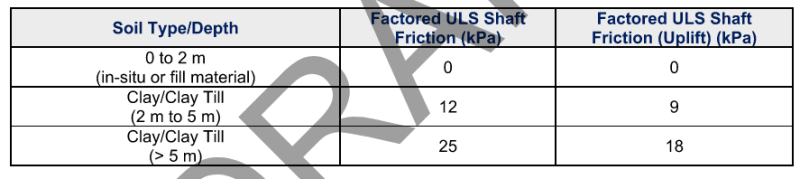
The foundation cylinder diameter is not to be over 1.6 m. The final output would look something like this.
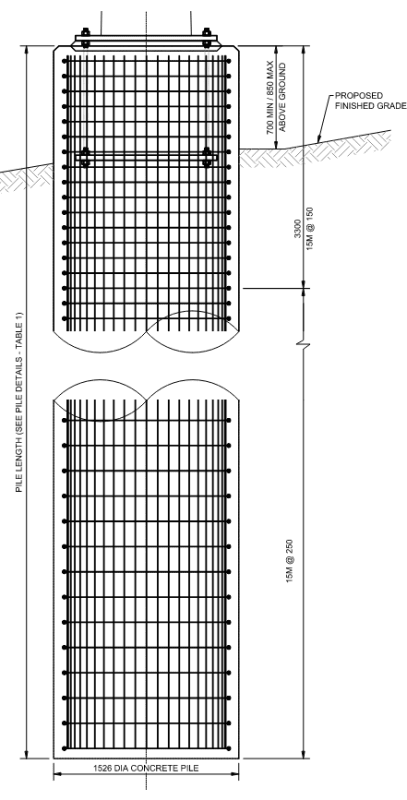
We have not done such a design before. If you are familiar with such design, kindly advise us on:
• How to design for torsion
• Comments on practical maximum depth of the cylinder
• Most critical thing to check in the design (What is the weakest link of the chain?)
If you could share design examples / calculations / drawings, that would also be highly appreciated.