Hello,
I would like to be given some practical engineering examples in which cylindricity is useful.
I am sure there are some useful cases, but I am not sure the examples I encountered use this tolerance efficiently.
In my opinion, in my workplace people tend to use this tolerance for holes and shafts that mate each other where there is no need for this.
When I asked them to explain this use, they said they want a "good" and "smooth" contact between the mating parts.
Here is a simplified illustration of 2 mated parts (section view):
Here you can see the nominal (in the CAD) clearance between the parts:
Here is a drawing view in which we can see the tolerance of each part:
In the last picture I marked the given cylindricity tolerance I am not quite sure is needed.
An entire contact isn't the design intent, but a minimum clearance between them.
So in my opinion, as long as there is a clearance the shape limit isn't critical.
I am looking forward to your advice.
Thanks!
I would like to be given some practical engineering examples in which cylindricity is useful.
I am sure there are some useful cases, but I am not sure the examples I encountered use this tolerance efficiently.
In my opinion, in my workplace people tend to use this tolerance for holes and shafts that mate each other where there is no need for this.
When I asked them to explain this use, they said they want a "good" and "smooth" contact between the mating parts.
Here is a simplified illustration of 2 mated parts (section view):
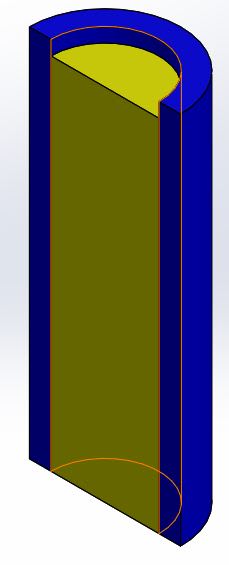
Here you can see the nominal (in the CAD) clearance between the parts:
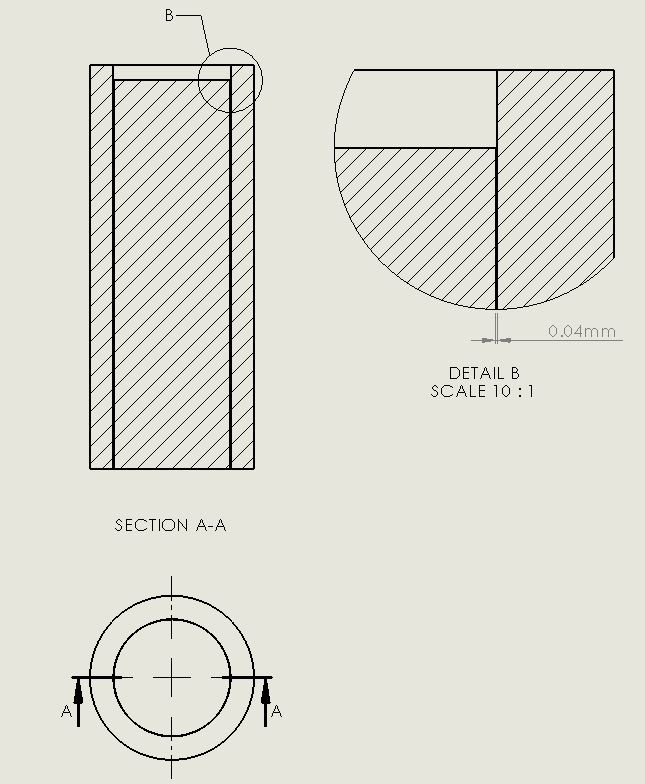
Here is a drawing view in which we can see the tolerance of each part:
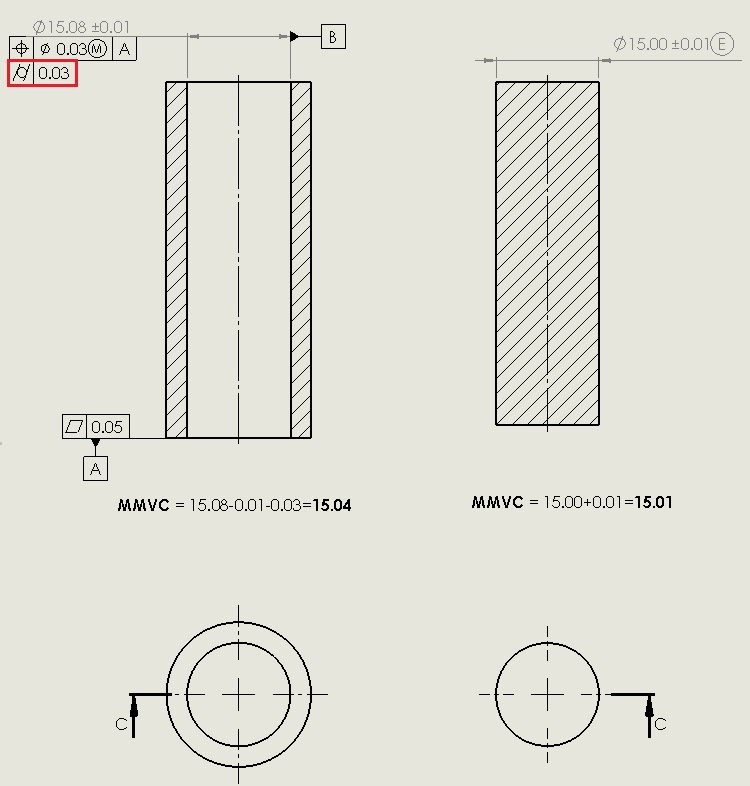
In the last picture I marked the given cylindricity tolerance I am not quite sure is needed.
An entire contact isn't the design intent, but a minimum clearance between them.
So in my opinion, as long as there is a clearance the shape limit isn't critical.
I am looking forward to your advice.
Thanks!