The picture below is a recent repair job that I worked on. Single story commercial building in a 155 mph (ult) wind zone. Over 60% of the gable end wall was compromised. The fix was both presciptive and engineered. Any thoughts on what you might do?
I guess this is a good example of "What not to do as an electrician" or any other trades person for that matter.
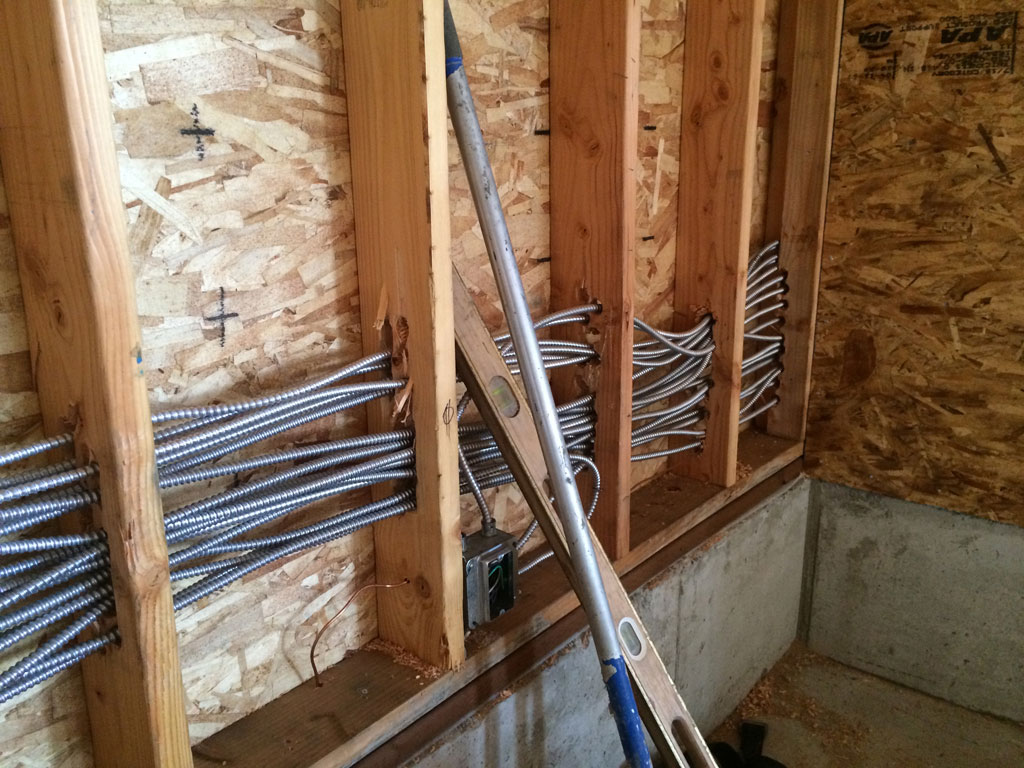
I guess this is a good example of "What not to do as an electrician" or any other trades person for that matter.