SolarPrestige
Electrical
- Mar 4, 2020
- 38
Looking at the attached photos, what's your first thought about what has failed? This cell set off an aspirated smoke detection early alarm. Heat damage (bad connection) or arcing damage (escaping from contactor) or something else?
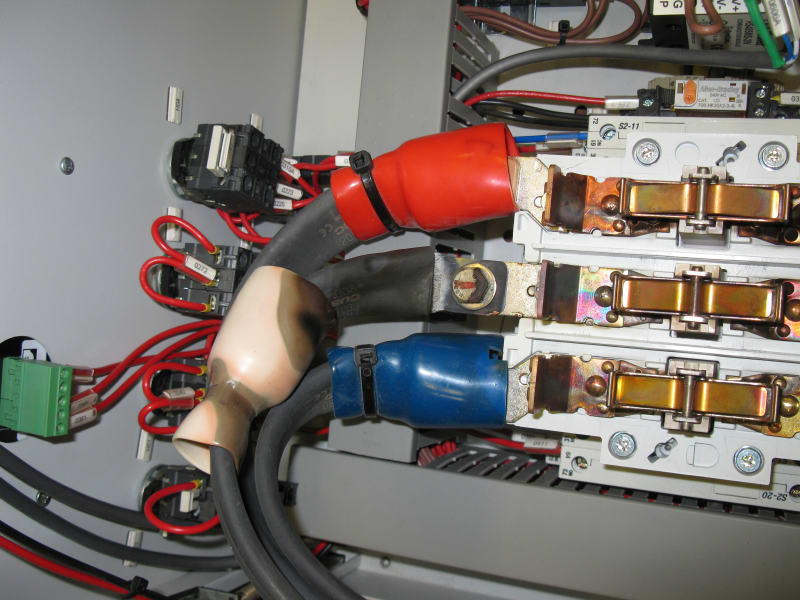
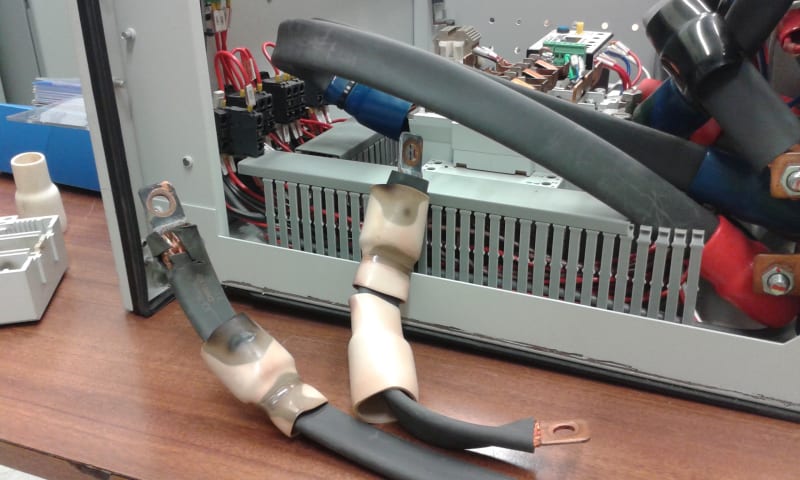