I started working with a new group, and they use a different GD&T datum order than I feel is correct.
I am used to the primary datum being listed as the flat plane (example 1), and the secondary datums placing the object/feature in said plane.
They use the planar datum as the tertiary datum (example 2)
I can't find anything specifically saying the planar datum is always the first datum, but in my head that is a rule...
I am used to the primary datum being listed as the flat plane (example 1), and the secondary datums placing the object/feature in said plane.
They use the planar datum as the tertiary datum (example 2)
I can't find anything specifically saying the planar datum is always the first datum, but in my head that is a rule...
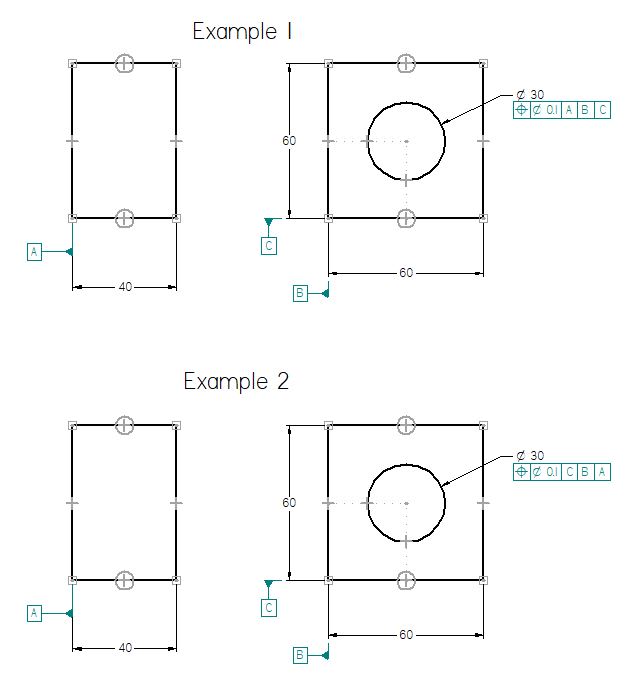