Septentrion
Electrical
Hi, I'm technician in a steel plant. I'm French and my knowledge of the English language is lacking (Sorry !)
It's my first post here but I often read the topics of this forum.
The context of my subject :
- a cold rolling mill with 5 stands.
- Each stand is driven by 2 motors, separated excitations, same shaft, made by Westinghouse in 70's.
- Stand 1 is 3000HP, 700V, 3440A, 150 RPM nominal speed - 150A field current
- Stands 2 to 5 are 4000HP, 800V, 4540A, 280 RPM nominal speed - 100A field current
- each motor has compensating windings.
The issue :
At low speed, high armature current causes high amplitude oscillations on field's current. There is no issue with field's current regulator : I made a test in open loop to verify.
The amplitude of oscillations decrease quickly with speed.
I found that the commutator's state have a big influence on these oscillations. Grinding the commutator leads to canceled the oscillations. In fact, oscillations are always present but amplitude is negligible
The frequency of oscillations is 12 times the motor speed for stands 2 to 5. It deals with the number of poles.
The frequency of oscillations is 10 times the motor speed for stand 1. It deals with the number of poles too.
You can see thereafter some curves. The first show the current reference for stand 4 (it's for the stand, so for each motor, it must be divided per 2). The second show the voltage for each motor. The third show field current for each motor. The last show the motors speed in RPM)
My question : how could armature's current could have an effect on field's current (I know the effect on field's flux) ?
It's my first post here but I often read the topics of this forum.
The context of my subject :
- a cold rolling mill with 5 stands.
- Each stand is driven by 2 motors, separated excitations, same shaft, made by Westinghouse in 70's.
- Stand 1 is 3000HP, 700V, 3440A, 150 RPM nominal speed - 150A field current
- Stands 2 to 5 are 4000HP, 800V, 4540A, 280 RPM nominal speed - 100A field current
- each motor has compensating windings.
The issue :
At low speed, high armature current causes high amplitude oscillations on field's current. There is no issue with field's current regulator : I made a test in open loop to verify.
The amplitude of oscillations decrease quickly with speed.
I found that the commutator's state have a big influence on these oscillations. Grinding the commutator leads to canceled the oscillations. In fact, oscillations are always present but amplitude is negligible
The frequency of oscillations is 12 times the motor speed for stands 2 to 5. It deals with the number of poles.
The frequency of oscillations is 10 times the motor speed for stand 1. It deals with the number of poles too.
You can see thereafter some curves. The first show the current reference for stand 4 (it's for the stand, so for each motor, it must be divided per 2). The second show the voltage for each motor. The third show field current for each motor. The last show the motors speed in RPM)
My question : how could armature's current could have an effect on field's current (I know the effect on field's flux) ?
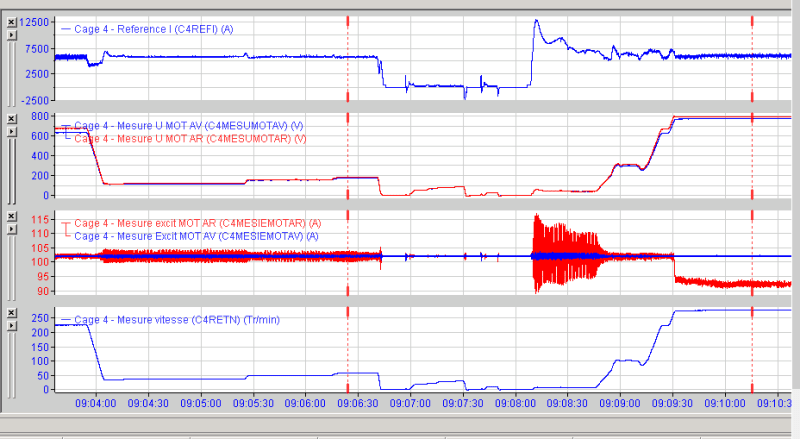