amazing azza
Industrial
- Apr 26, 2017
- 130
Background.
We have a deaerator, as shown in the diagram below. The dome features permanently mounted waterfall trays. The problem with it has been that it cannot receive cold make-up. Shortly after cold makeup water starts flowing, loud implosions are heard coming from the top of the dome, and the vent pukes up water. This does not happen while running at 100% condensate return.
Initially, the recirculating pump and the dome steam supply were not installed/connected. Thus, the problem was blamed on their absence. Recently, the missing items have been added. However, the problem persists, albeit now a slow stream of makeup is able to be introduced (0.75 m3/h out of a nominal 5 m3/h).
Detailed description of the symptoms.
Typical operating conditions are TT = 105 C, PI = 0.15 barg. The storage tank being regulated by the TT-CV combo to remain at those values. The temperatures in the waterfall sections are usually around TI1 = 96 C, TI2 = 105 C, TI3 = 105 C. If at this state one starts introducing cold makeup, the values remain roughly the same, with the exception of TI1, which falls rapidly. Before any change in storage tank temperature is detected, vacuum implosions are already occurring.
An improvement can be made by sending steam (3 barg) to the dome supply (PI rises to 0.5 barg), running the recirc pump (Q=5 m3/h), and opening the vent wider so that instead of a "wisp" of steam it becomes a small jet. With these settings, 0.75 m3/h of cold (30 C) makeup can be continuously introduced. The storage tank temperature rises to 110 C, and the sparging steam is never added in response to the makeup. The internal pressure remains at 0.5 barg, and the top tray temperature TI1 stabilizes at 102-104 C. If either the dome steam or the venting rate are reduced, vacuum implosions occur soon after. If the cold makeup rate is increased even slightly, implosions occur even quicker.
Question.
Why is the makeup rate so limited? What can be done to increase it?
My own thoughts.
I have looked through catalogs of manufacturers supplying similar systems and one thing stood out to me. There are "unlabeled rectangles" passing through their waterfall reservoirs (see below). Are these pressure equalizing bypasses? If so, our dome does not have anything similar (see below).
Existing:
Manufacturer 1:
Manufacturer 2:
We have a deaerator, as shown in the diagram below. The dome features permanently mounted waterfall trays. The problem with it has been that it cannot receive cold make-up. Shortly after cold makeup water starts flowing, loud implosions are heard coming from the top of the dome, and the vent pukes up water. This does not happen while running at 100% condensate return.
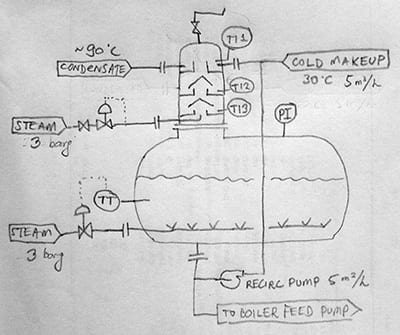
Initially, the recirculating pump and the dome steam supply were not installed/connected. Thus, the problem was blamed on their absence. Recently, the missing items have been added. However, the problem persists, albeit now a slow stream of makeup is able to be introduced (0.75 m3/h out of a nominal 5 m3/h).
Detailed description of the symptoms.
Typical operating conditions are TT = 105 C, PI = 0.15 barg. The storage tank being regulated by the TT-CV combo to remain at those values. The temperatures in the waterfall sections are usually around TI1 = 96 C, TI2 = 105 C, TI3 = 105 C. If at this state one starts introducing cold makeup, the values remain roughly the same, with the exception of TI1, which falls rapidly. Before any change in storage tank temperature is detected, vacuum implosions are already occurring.
An improvement can be made by sending steam (3 barg) to the dome supply (PI rises to 0.5 barg), running the recirc pump (Q=5 m3/h), and opening the vent wider so that instead of a "wisp" of steam it becomes a small jet. With these settings, 0.75 m3/h of cold (30 C) makeup can be continuously introduced. The storage tank temperature rises to 110 C, and the sparging steam is never added in response to the makeup. The internal pressure remains at 0.5 barg, and the top tray temperature TI1 stabilizes at 102-104 C. If either the dome steam or the venting rate are reduced, vacuum implosions occur soon after. If the cold makeup rate is increased even slightly, implosions occur even quicker.
Question.
Why is the makeup rate so limited? What can be done to increase it?
My own thoughts.
I have looked through catalogs of manufacturers supplying similar systems and one thing stood out to me. There are "unlabeled rectangles" passing through their waterfall reservoirs (see below). Are these pressure equalizing bypasses? If so, our dome does not have anything similar (see below).
Existing:
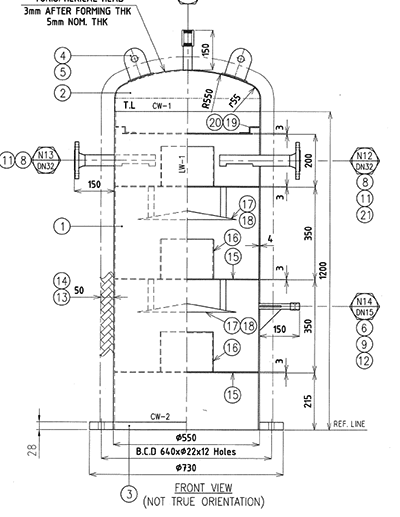
Manufacturer 1:

Manufacturer 2:
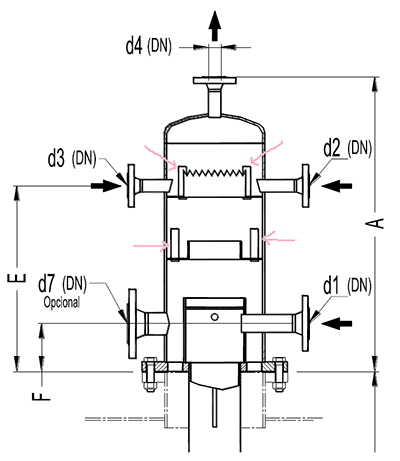