Mohsen_81
Mechanical
- Dec 14, 2020
- 26
Hi all,
Inspection shows a crack in the shell of the deaerator at the weld of the top platform support. Condition is as below.
-Deaerator, 3.5barg, SS304L, 10 yeas old
-4 top platform support leg, track on only one of them at 12 o'clock position.
-Please see the photo. we have marked the suggested positions for temporary support to work 3 years.
Please let me know your suggestion, tips, and concerns.
Inspection shows a crack in the shell of the deaerator at the weld of the top platform support. Condition is as below.
-Deaerator, 3.5barg, SS304L, 10 yeas old
-4 top platform support leg, track on only one of them at 12 o'clock position.
-Please see the photo. we have marked the suggested positions for temporary support to work 3 years.
Please let me know your suggestion, tips, and concerns.
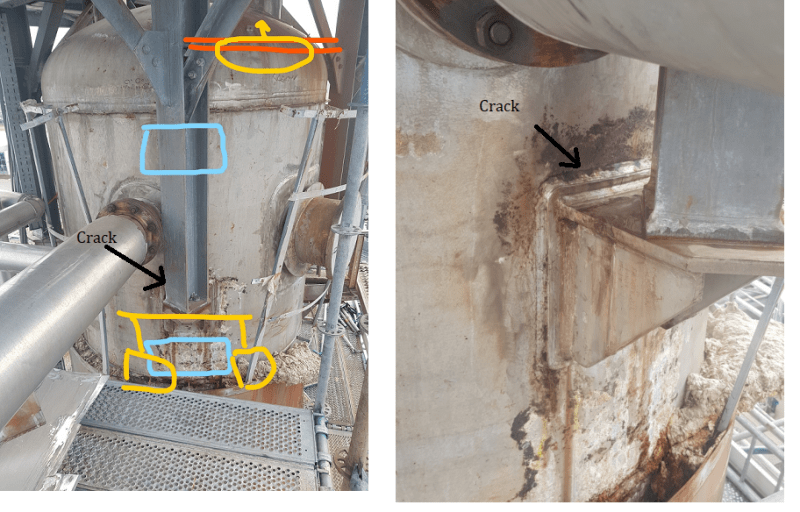