Samwise Gamgee
Structural
- Oct 7, 2021
- 118
I have a 3" metal deck on roof. For the closure of the deck, I was planning on using an angle like shown in the picture. I have a couple of questions
[ul]
[li]Is it safe to say that the deck angle only acts as a chord member[/li]
[li]How do I design the weld between the edge angle and the deck ? I have seen it shown as 1/4" fillet weld at 3-12. I am assuming that means 3" per every 12" . What determines if this is adequate ? [/li]
[/ul]
[ul]
[li]Is it safe to say that the deck angle only acts as a chord member[/li]
[li]How do I design the weld between the edge angle and the deck ? I have seen it shown as 1/4" fillet weld at 3-12. I am assuming that means 3" per every 12" . What determines if this is adequate ? [/li]
[/ul]
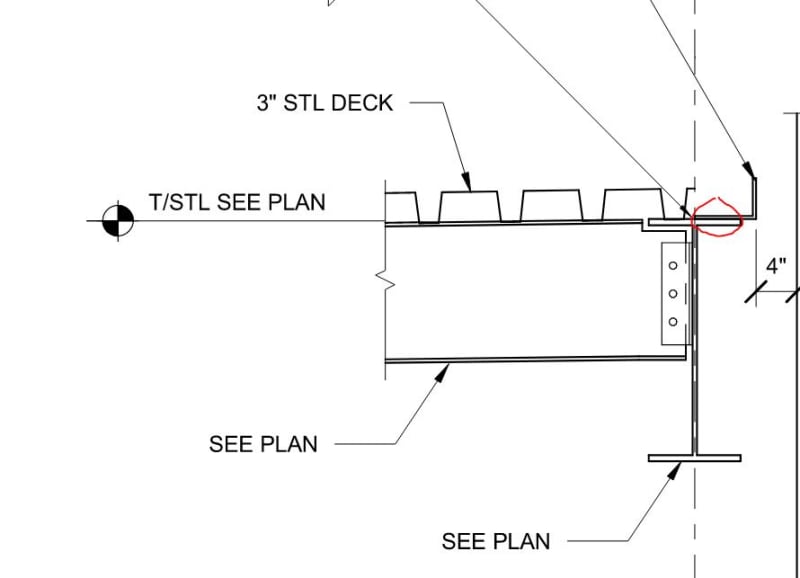