xMeck
Electrical
- Nov 5, 2019
- 9
I was just curious how far off I am with my current design from making my desired design. I want to produce a Three phase squirrel cage induction motor but I cant say I'm 100% confident on how to do so, currently I just want to run the design with default parameters before I start to change the values of the friction coefficient, rated stator voltage, number of poles and the rated frequency. The design is a small section of what I need to do compared to the testing although I dont have a clue how to fully make the system into a three phase squirrel induction motor as it seems I cant find anything similar anywhere. Just to add I am using PLECS 4.4.4 software.
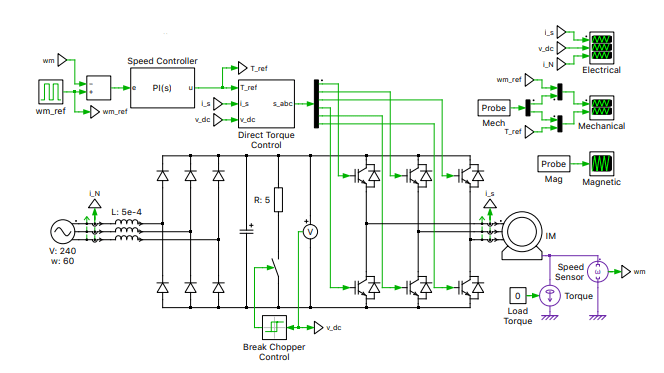