HanStrulo
Civil/Environmental
- Apr 16, 2021
- 117
Hi Everyone,
I have an elementary question about angles in bending.
I have an angle in bending. Length of the angle is about 15" and the load is applied in the middle of the angle. (There is a sketch below).
My question is: since the load is on the middle of one leg and not on the geometric center of principle axis. How to calculate the bending resistance of the angle? do i have to check something else other than bending?
Thanks alot
I have an elementary question about angles in bending.
I have an angle in bending. Length of the angle is about 15" and the load is applied in the middle of the angle. (There is a sketch below).
My question is: since the load is on the middle of one leg and not on the geometric center of principle axis. How to calculate the bending resistance of the angle? do i have to check something else other than bending?
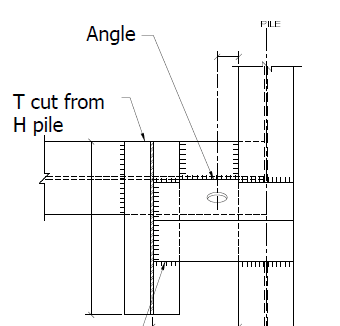
Thanks alot