Vibration Lover
Civil/Environmental
Is there any reasons or Pro &con for design of bridge span not flat?
In case I have to design the elevated like a frame bridge below?
What shall I consider and what shall the dynamic impact factor used?
Sorry for not a nice sketch
Thanks for sharing
In case I have to design the elevated like a frame bridge below?
What shall I consider and what shall the dynamic impact factor used?
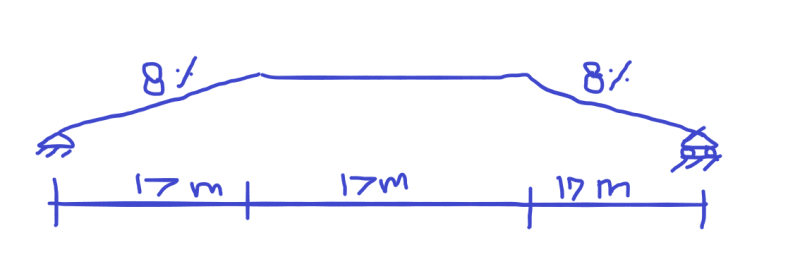
Sorry for not a nice sketch
Thanks for sharing