BufordTJustice
Mechanical
Hello-
I have a flat roof onto which I am interested in installing some solar panel arrays. As I am in a high wind area (design is ~145 mph), I either need to penetrate the roof 50+ times to anchor the panel mounting rails, or use a ballasted system and avoid the penetrations altogether.
I am leaning towards the ballasted approach as it not only eliminates the cost of large number of roof penetrations but also the opportunities for leaks which will certainly become more likely with so many penetrations. The ballasted approach also removes uplift loads from being applied to the roof structure itself (as the ballast is sized accordingly to handle this).
In any case, the specifics of the roof are as follows----
The roof is flat (covered with a single ply TPO membrane over 1/2" iso board, which is over 1/2" plywood sheathing). The trusses are parallel chord type and are spaced 24" OC across the roof and are comprised of 2x4 members. The span between vertical supports is ~12 ft and the depth of the truss (measured between the outside of both the top and bottom chords) is ~68" A photo is below.
.
Is there an easy way to determine the maximum load in psf this roof could be expected to support? I'm going for permit for the solar system this is going to be question 1 that I have to answer. Thanks for the help!
I have a flat roof onto which I am interested in installing some solar panel arrays. As I am in a high wind area (design is ~145 mph), I either need to penetrate the roof 50+ times to anchor the panel mounting rails, or use a ballasted system and avoid the penetrations altogether.
I am leaning towards the ballasted approach as it not only eliminates the cost of large number of roof penetrations but also the opportunities for leaks which will certainly become more likely with so many penetrations. The ballasted approach also removes uplift loads from being applied to the roof structure itself (as the ballast is sized accordingly to handle this).
In any case, the specifics of the roof are as follows----
The roof is flat (covered with a single ply TPO membrane over 1/2" iso board, which is over 1/2" plywood sheathing). The trusses are parallel chord type and are spaced 24" OC across the roof and are comprised of 2x4 members. The span between vertical supports is ~12 ft and the depth of the truss (measured between the outside of both the top and bottom chords) is ~68" A photo is below.
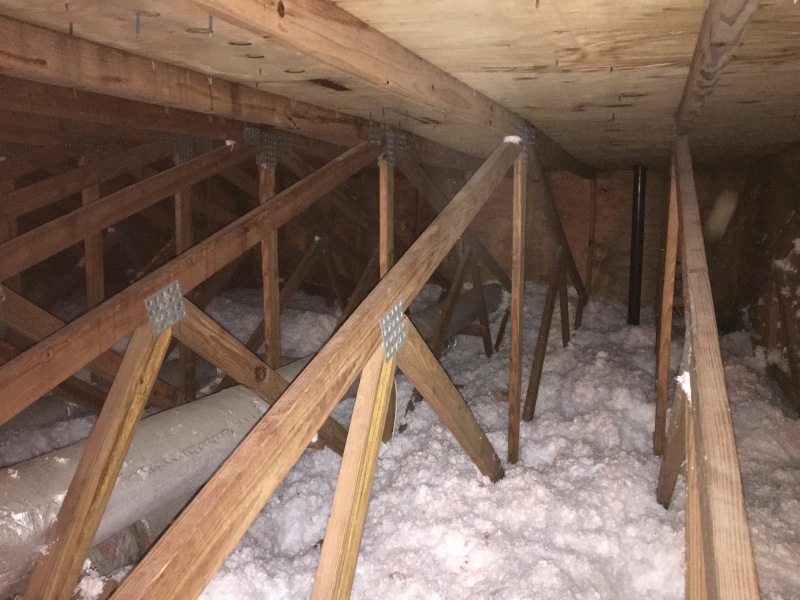
Is there an easy way to determine the maximum load in psf this roof could be expected to support? I'm going for permit for the solar system this is going to be question 1 that I have to answer. Thanks for the help!