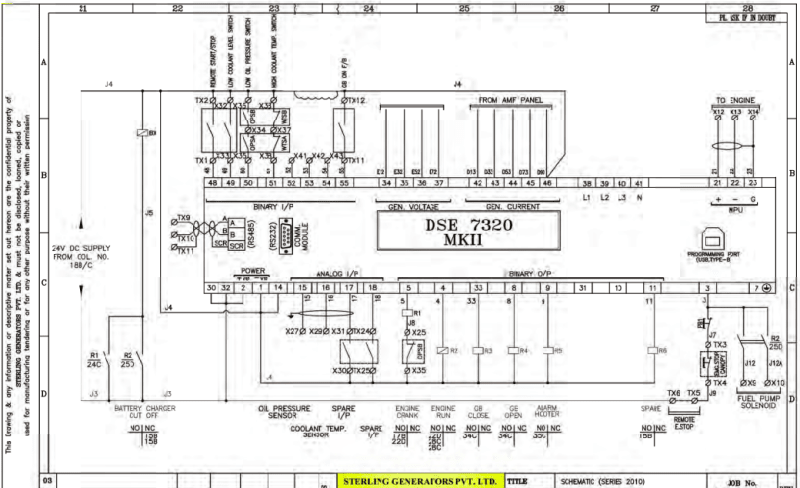
This is an scheme of LCP (Local Control Panel) in DG SET. Here the controller gets input from AMF panel. I was just wondering what is difference between DG Crank & DG Run relay R1 & R2 (just asking in general about the sequence of operation).
As I have read a DC supply from battery needs to give command to starter motor (DC) through solenoid coil. This cranks the crank shaft & starts the combustion/ expansion piston process. So what is the DG Run/ DG Crank relay for? Does it have to do with Fuel Inlet?
Also in the given scheme the controller gives o/p 24V to the relays. But what if an emergency situation & controller fails to give command, is there a possibility to loop & provide direct 24V to relay?
Best!