Im using software Tower 6 for FEM.
I have modeled 3 frames (same geometry but different cross sections/material for each frame):
MODEL 1: concrete 300/300 mm
MODEL 2: concrete 200/200 mm
MODEL 3: steel H section
Im wondering why do I get so different results for each model? Looks like software takes into account the stiffnes of columns/beam (based on geometry and material)when calculating internal forces in elements?
I dont like it since you can design elements based on lets say model 1, but when you choose to change a section in the middle of design - lets say from 300/300 cm to 300/350 mm and you have different internal forces (moments, shear)...
How do you guys model stuff like this?
As far as I know, internal forces should be the same for each model (if we dont consider self weight of elements) - forces should depend on geometry of model and loads only...
I have modeled 3 frames (same geometry but different cross sections/material for each frame):
MODEL 1: concrete 300/300 mm
MODEL 2: concrete 200/200 mm
MODEL 3: steel H section
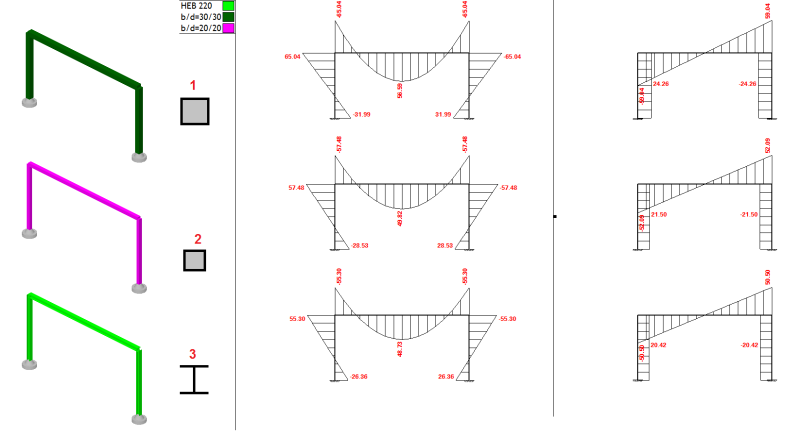
Im wondering why do I get so different results for each model? Looks like software takes into account the stiffnes of columns/beam (based on geometry and material)when calculating internal forces in elements?
I dont like it since you can design elements based on lets say model 1, but when you choose to change a section in the middle of design - lets say from 300/300 cm to 300/350 mm and you have different internal forces (moments, shear)...
How do you guys model stuff like this?
As far as I know, internal forces should be the same for each model (if we dont consider self weight of elements) - forces should depend on geometry of model and loads only...