I'm seeking some advice regarding a difficult concrete repair that I'm undertaking. While I'm interested to discuss the possible causes of the problem, we're mostly just in problem solving mode at this time: how best to responsibly investigate and fix this. For context, everything that follows was copied from an email that I sent to our local Sika rep.
My cliff notes:
1) This is predominantly at column locations.
2) We suspect that uncleared snow on the form deck was likely the culprit here, perhaps in combination with vibration issues.
3) All of the stud rails are too low for cover in their current state. We’re contemplating additional concrete cast below the existing soffit level.
4) We have some concern for the snow having melted into the concrete and messed with the water content locally.
5) We have reason to believe that we have this same issue not just beside our columns but above them. This creates a soffit repair access problem.
6) As you can see, these areas are quite congested with two layers of bottom steel, integrity steel in two directions, and stud rails. It’s a lot of stuff to climb over top of with a repair.
7) My instinct with this kind of thing is to chip concrete away at least 1” above the uppermost rebar before coming back with repair material. That, both for repair longevity and for getting a convincing bond between the bars, the repair material, and the existing substrate. As you mentioned, Hilti has confidence in it’s partial depth repair solutions. You’ll need to dust your salesman hat off and see if you can convince me of the same as I’ve no doubt that our contractor would prefer that.
Here’s a rough outline of what the engineer in me has been contemplating as a hard line repair strategy:
1) Sandblast the soffit to clean things and remove any material that might have been weakened by a higher than normal water content.
2) Hydrodemolish the slab through its entire thickness at areas where we will be doing significant repair. This is not how we make friends.
3) Form new, drop panel-ish looking things below the existing concrete soffit to get us right with cover requirements. Vertical dowels etc.
4) Install our repair material from the top. Low/no shrinkage stuff that flows well.
My cliff notes:
1) This is predominantly at column locations.
2) We suspect that uncleared snow on the form deck was likely the culprit here, perhaps in combination with vibration issues.
3) All of the stud rails are too low for cover in their current state. We’re contemplating additional concrete cast below the existing soffit level.
4) We have some concern for the snow having melted into the concrete and messed with the water content locally.
5) We have reason to believe that we have this same issue not just beside our columns but above them. This creates a soffit repair access problem.
6) As you can see, these areas are quite congested with two layers of bottom steel, integrity steel in two directions, and stud rails. It’s a lot of stuff to climb over top of with a repair.
7) My instinct with this kind of thing is to chip concrete away at least 1” above the uppermost rebar before coming back with repair material. That, both for repair longevity and for getting a convincing bond between the bars, the repair material, and the existing substrate. As you mentioned, Hilti has confidence in it’s partial depth repair solutions. You’ll need to dust your salesman hat off and see if you can convince me of the same as I’ve no doubt that our contractor would prefer that.
Here’s a rough outline of what the engineer in me has been contemplating as a hard line repair strategy:
1) Sandblast the soffit to clean things and remove any material that might have been weakened by a higher than normal water content.
2) Hydrodemolish the slab through its entire thickness at areas where we will be doing significant repair. This is not how we make friends.
3) Form new, drop panel-ish looking things below the existing concrete soffit to get us right with cover requirements. Vertical dowels etc.
4) Install our repair material from the top. Low/no shrinkage stuff that flows well.
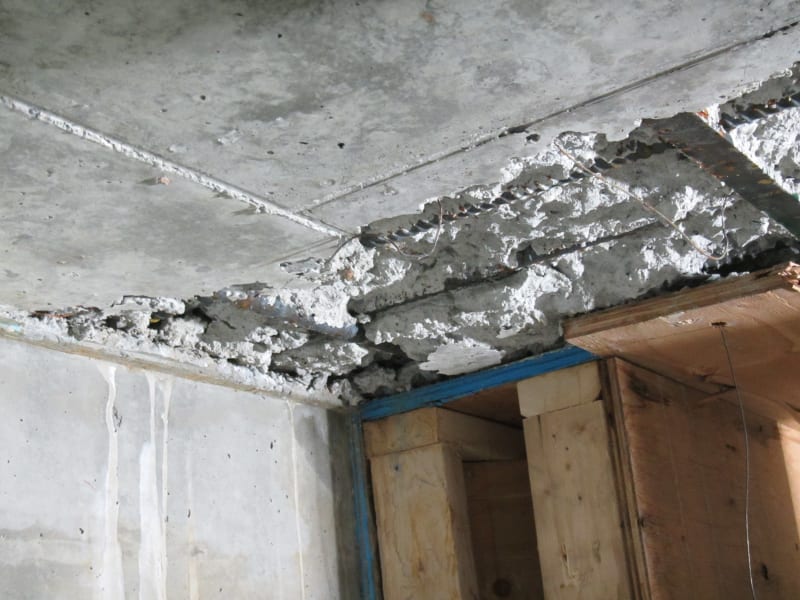
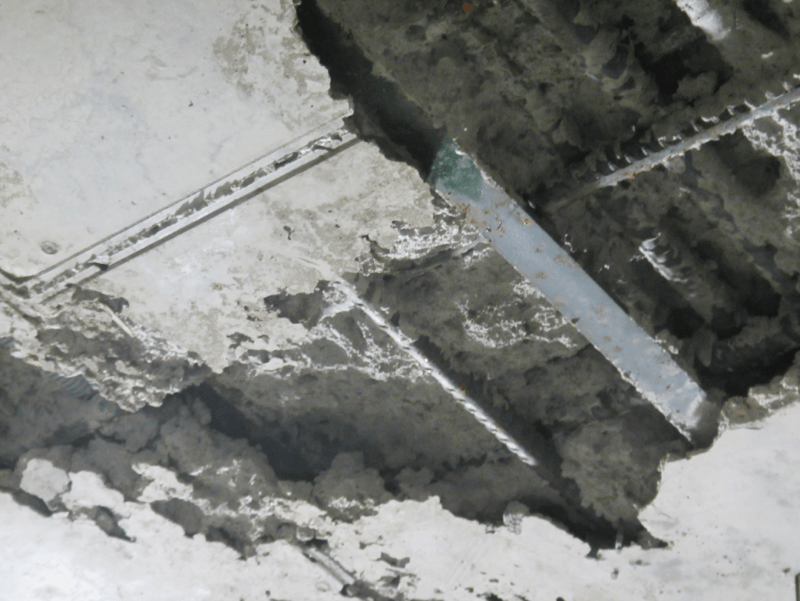
