Hello,
I have an Ultem 1000 Flange that has to be connected to a Titanium container with a screw made of steel.
I am presenting only a portion of the bolted joint for simplification:
First of all I have to point out that my preload is limited by the ULTEM 1000 and hence it's only preloaded to 2450N.
I was looking for a solution to 2 problems:
1. Preload decrease due to exposure to cold temperature (del_T=-25 celcius degrees).
2. Preload decrease due to the (unknown) ULTEM creep in compression.
As a result I thought that adding a "spring" element with a moderate stiffness may compensate the deflections with only quite small load decrease. So I decided (as a result of limited space) to try to use (for the first time) Disc Spring for this purpose, as described in the picture above.
I have some questions regarding this design:
1. Is there a problem of stacking 10 Disks in parallel?
I couldn't find an adequate standard Disk Spring (for a #10 bolt) that may give me such forces.
It's important to point out that I have a limitation of maximum outer diameter (of the Disk Spring) of 12 mm that isn't seen in the picture above, and that's why I can't use a massive disk spring.
2. Is there another elegant solution I didn't think of and that is preferable?
3. Just to make sure I have no mistake - is the ULTEM 1000 surface will have a reaction force that is equal to the bolt axial load (that is equal to the equivalent spring force exerted by the induced deflection)? I read somewhere that as a result of internal friction between the disks the ULTEM 1000 experiences a lower force than the exerted force (of the bolt), but when I drew a Force Body Diagram I found out that for an equilibrium the reaction in the ULTEM surface has to be equal to the bolt axial force.
I am looking forward to your good advice!
Have a nice day
I have an Ultem 1000 Flange that has to be connected to a Titanium container with a screw made of steel.
I am presenting only a portion of the bolted joint for simplification:
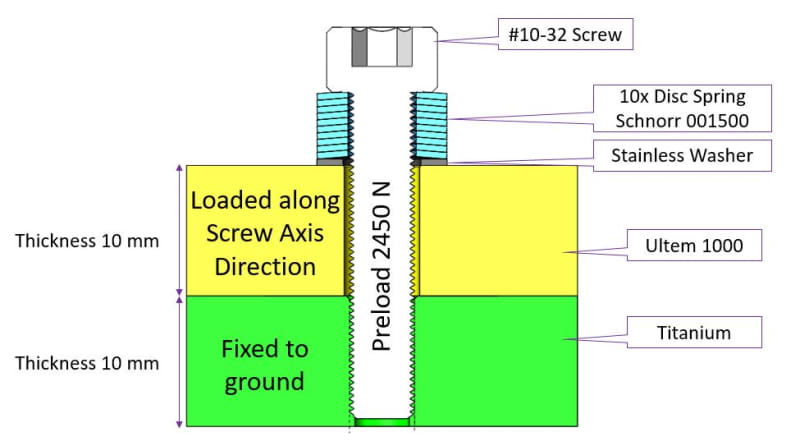
First of all I have to point out that my preload is limited by the ULTEM 1000 and hence it's only preloaded to 2450N.
I was looking for a solution to 2 problems:
1. Preload decrease due to exposure to cold temperature (del_T=-25 celcius degrees).
2. Preload decrease due to the (unknown) ULTEM creep in compression.
As a result I thought that adding a "spring" element with a moderate stiffness may compensate the deflections with only quite small load decrease. So I decided (as a result of limited space) to try to use (for the first time) Disc Spring for this purpose, as described in the picture above.
I have some questions regarding this design:
1. Is there a problem of stacking 10 Disks in parallel?
I couldn't find an adequate standard Disk Spring (for a #10 bolt) that may give me such forces.
It's important to point out that I have a limitation of maximum outer diameter (of the Disk Spring) of 12 mm that isn't seen in the picture above, and that's why I can't use a massive disk spring.
2. Is there another elegant solution I didn't think of and that is preferable?
3. Just to make sure I have no mistake - is the ULTEM 1000 surface will have a reaction force that is equal to the bolt axial load (that is equal to the equivalent spring force exerted by the induced deflection)? I read somewhere that as a result of internal friction between the disks the ULTEM 1000 experiences a lower force than the exerted force (of the bolt), but when I drew a Force Body Diagram I found out that for an equilibrium the reaction in the ULTEM surface has to be equal to the bolt axial force.
I am looking forward to your good advice!
Have a nice day