Hamza 13
Student
- Sep 8, 2021
- 7
Hello,
I have some problems with my Abaqus model, the job ran successfully and complete the time but the result is not as desired, the model shows a deformable shape and the hysteresis curve failed to get symmetrical loops.
the model is a metallic damper under cyclic loading.
step= static general, load: fixed end at left, loading at right (cyclic loading as tabular data) contains three different amplitudes, each amplitude was repeated 3 times, and sliding hinge either in the right(all fixed except the loading direction).
mesh: C3D6 is used ( sweep wedge elements) were no errors or warnings by using the mesh verify tool.
looking for your answers, and suggestions to get the right result.
pic attached shows the deformable shape of the system as shown there was buckling in the steel core and that is the cause of not getting the right hysteresis curve.
Best regards.
I have some problems with my Abaqus model, the job ran successfully and complete the time but the result is not as desired, the model shows a deformable shape and the hysteresis curve failed to get symmetrical loops.
the model is a metallic damper under cyclic loading.
step= static general, load: fixed end at left, loading at right (cyclic loading as tabular data) contains three different amplitudes, each amplitude was repeated 3 times, and sliding hinge either in the right(all fixed except the loading direction).
mesh: C3D6 is used ( sweep wedge elements) were no errors or warnings by using the mesh verify tool.
looking for your answers, and suggestions to get the right result.
pic attached shows the deformable shape of the system as shown there was buckling in the steel core and that is the cause of not getting the right hysteresis curve.
Best regards.
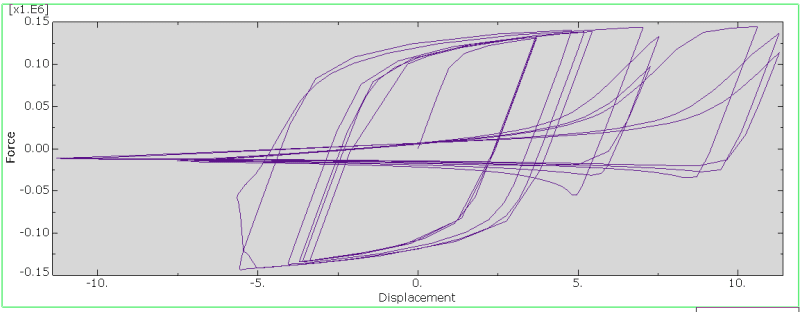

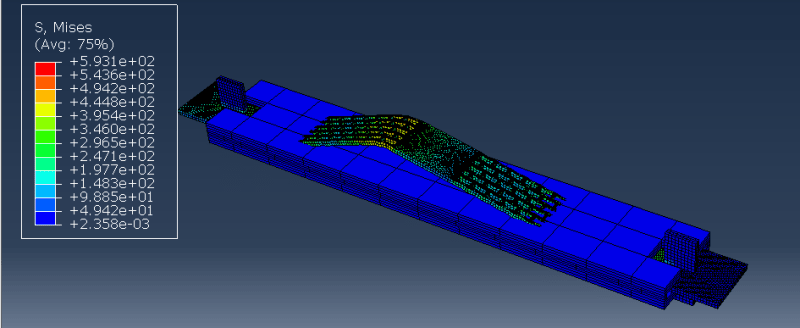