Hi there,
We have a closing aluminium shell. It is connected on an aluminium plate using screws and an o-ring. Inside there is a nitrogen atmosphere, overpressure, like 20mbar. We might change the shell to plastic. We have tested this, no problem.
We would like to divide the shell into two parts in order to ease the future maintenance.
What can we do to have 3 parts and be able to get them sealed? There will be a point where 3 edges join.
Here a sketch
thanks
We have a closing aluminium shell. It is connected on an aluminium plate using screws and an o-ring. Inside there is a nitrogen atmosphere, overpressure, like 20mbar. We might change the shell to plastic. We have tested this, no problem.
We would like to divide the shell into two parts in order to ease the future maintenance.
What can we do to have 3 parts and be able to get them sealed? There will be a point where 3 edges join.
Here a sketch
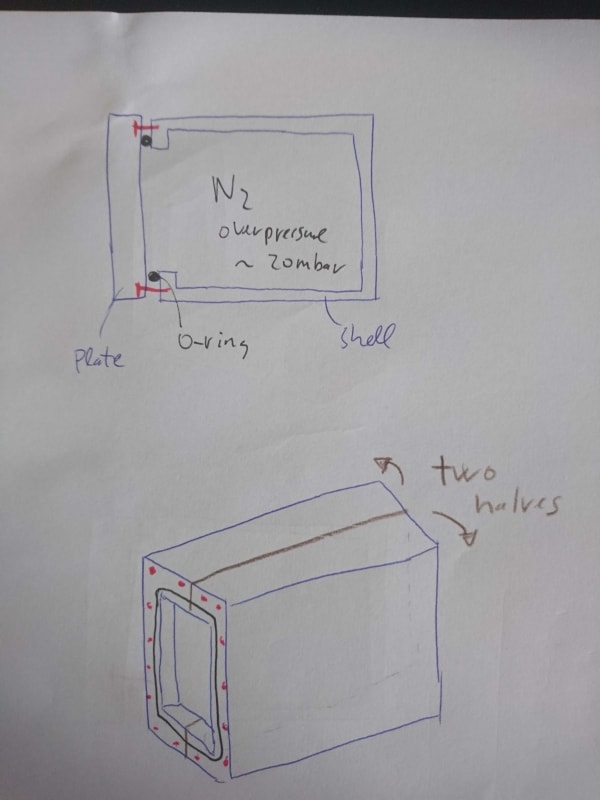
thanks