ExpatIreland
Industrial
This is a new thread from my initial 'Phase Converter question - 1ph to 3ph'. (To all those that answered thanks very much). Instead of continuing that thread I thought it best to start a fresh one.
I have more data now. Our 3 phase 7.5hp/5/5kw coffee grinder's motor plate is at this link so you can see the specs on it.
I am going to run the grinder on house current (IRELAND) of 230V/50HZ.
The load on the motor will be steady and there will only be this one piece of equipment being serviced by the converter/inverter.
One friend, who runs a lot of 3ph equipment says to buy an INVERTER to change the power from 1ph to 3ph. He says the power delivered will be more steady and my motor will last longer. Two or three other people say the exact opposite. They say the INVERTER will have a lot of distortion and won't be as 'harmonic' as the ROTARY/DIGITAL converter.
Another says I need a ROTARY PHASE CONVERTER because if the input to the INVERTER is 230V I'll only get 230V coming out the other end.
Another says I should look into a DIGITAL PHASE CONVERTER as it is better than the ROTARY even though it costs about £400 more. He says the DIGITAL converter is quieter and delivers more even power.
The ROTARY PHASE CONVERTER company says they're the best way to go.
The DIGITAL PHASE CONVERTER company says they're the best way to go.
I'm completely confused. What's the difference between ROTARY and DIGITAL converters, and which would you purchase given the information provided? And if you lean toward the DIGITAL CONVERTER is the higher price justified? If you need additional information please let me know.
Thank you in advance for your insights!
William
I have more data now. Our 3 phase 7.5hp/5/5kw coffee grinder's motor plate is at this link so you can see the specs on it.
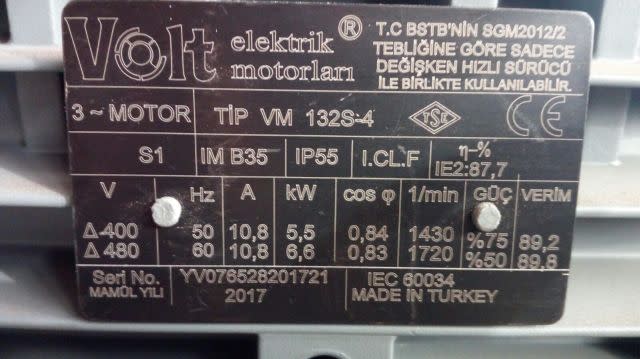
I am going to run the grinder on house current (IRELAND) of 230V/50HZ.
The load on the motor will be steady and there will only be this one piece of equipment being serviced by the converter/inverter.
One friend, who runs a lot of 3ph equipment says to buy an INVERTER to change the power from 1ph to 3ph. He says the power delivered will be more steady and my motor will last longer. Two or three other people say the exact opposite. They say the INVERTER will have a lot of distortion and won't be as 'harmonic' as the ROTARY/DIGITAL converter.
Another says I need a ROTARY PHASE CONVERTER because if the input to the INVERTER is 230V I'll only get 230V coming out the other end.
Another says I should look into a DIGITAL PHASE CONVERTER as it is better than the ROTARY even though it costs about £400 more. He says the DIGITAL converter is quieter and delivers more even power.
The ROTARY PHASE CONVERTER company says they're the best way to go.
The DIGITAL PHASE CONVERTER company says they're the best way to go.
I'm completely confused. What's the difference between ROTARY and DIGITAL converters, and which would you purchase given the information provided? And if you lean toward the DIGITAL CONVERTER is the higher price justified? If you need additional information please let me know.
Thank you in advance for your insights!
William