I am on the board of directors for small condominium in Canada. The building was built in 1979, it is wood-frame construction and has a flat (i.e. low-slope) roof.
Recently we had a roof consultant inspect the roof in preparation for replacement of the weatherproofing membrane, that covers the roof, next year. When looking at the framing below the plywood deck of the roof the consultant noticed what he described as questionable construction work and recommended that we hire a structural engineer to check it out and determine it's structural integrity.
The consultant made his observations of the roof framing from a hatch opening that penetrates through the roof structure making it possible to see below the deck. I have attached four photographs taken on opposite sides of the hatch opening, looking down the cavities between cross-strapping members that support the deck. On the photos I have indicated the consultant’s comments about the construction work.
My questions for this forum:
What do you think about the quality of the construction work shown in the photos, specifically the attachments between the components of the roof - the plywood deck, the tapered 2x4 cross-strapping members and the 2x10 joists?
Does it look like typical construction work for a wood-framed building?
Do you think the consultant’s comments about the structural integrity of the roof are justified?
Recently we had a roof consultant inspect the roof in preparation for replacement of the weatherproofing membrane, that covers the roof, next year. When looking at the framing below the plywood deck of the roof the consultant noticed what he described as questionable construction work and recommended that we hire a structural engineer to check it out and determine it's structural integrity.
The consultant made his observations of the roof framing from a hatch opening that penetrates through the roof structure making it possible to see below the deck. I have attached four photographs taken on opposite sides of the hatch opening, looking down the cavities between cross-strapping members that support the deck. On the photos I have indicated the consultant’s comments about the construction work.
My questions for this forum:
What do you think about the quality of the construction work shown in the photos, specifically the attachments between the components of the roof - the plywood deck, the tapered 2x4 cross-strapping members and the 2x10 joists?
Does it look like typical construction work for a wood-framed building?
Do you think the consultant’s comments about the structural integrity of the roof are justified?
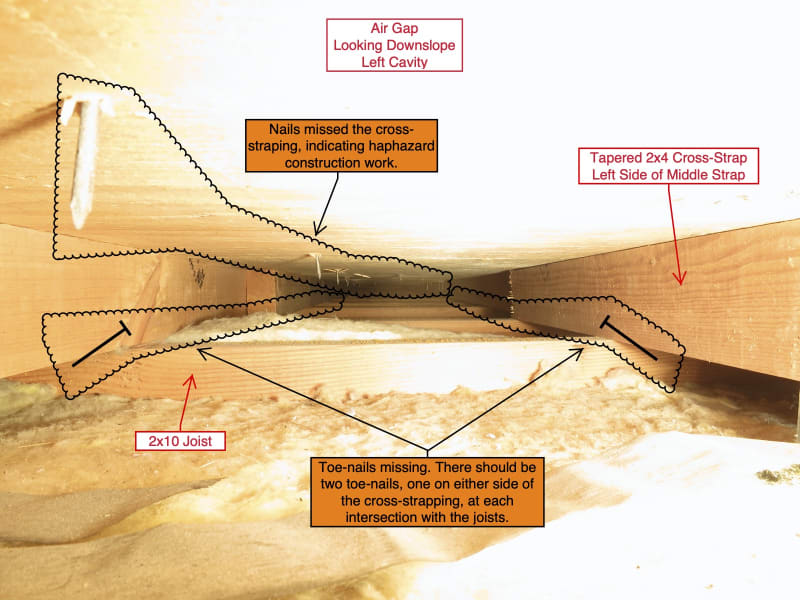
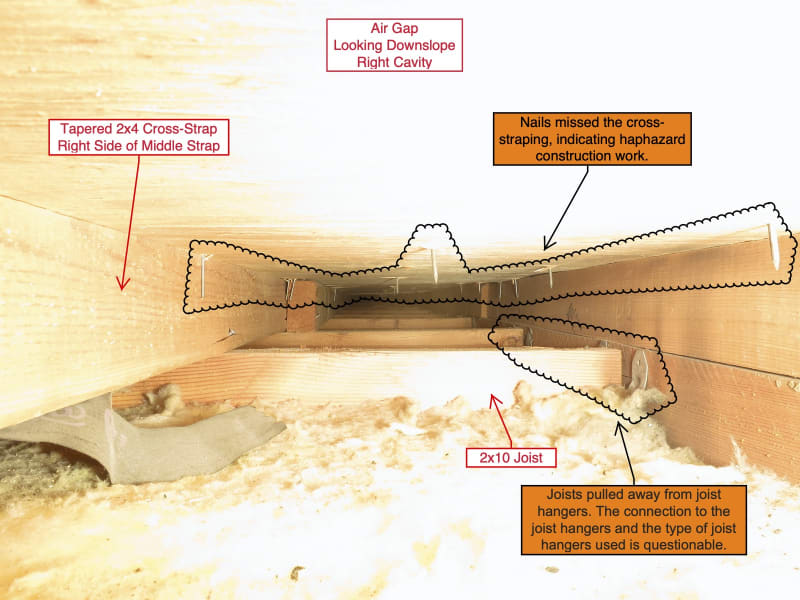
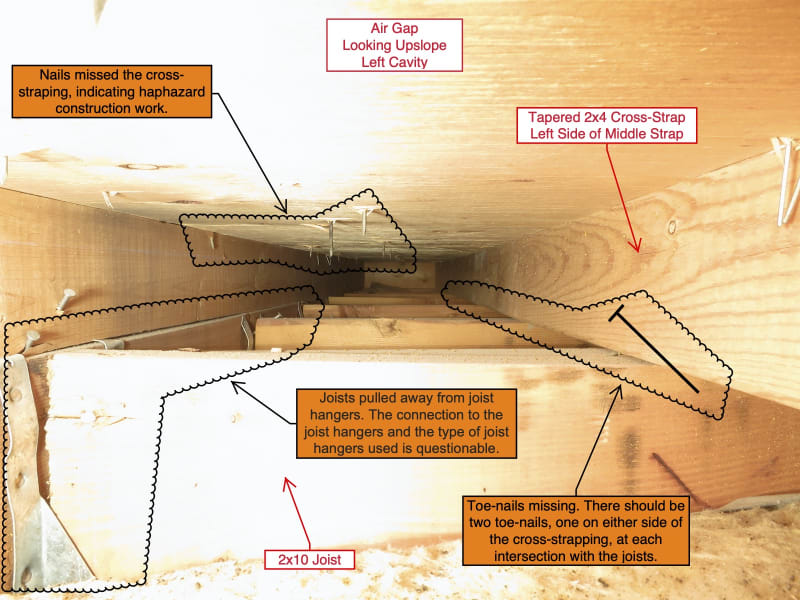
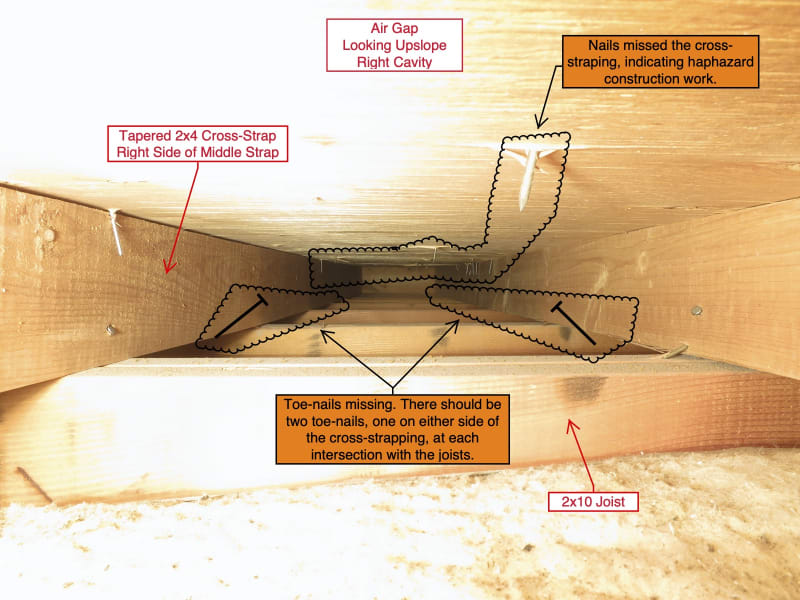