Consider a clevis with a bolt going through it, with an elastomeric washer on both sides to prevent rotation.
In terms of maximizing the friction, I don't think the washer's diameter matters because friction doesn't care about surface area (assuming a constant pre-load from the bolt and that the washer is always completely covered by the bolt/nut heads for even clamping).
The counter-argument is that with a larger diameter washer, the resistance to rotation is greater since it's a greater moment (the friction is acting further away from the axis of rotation). But surely that's countered by the frictional force being lower throughout making this a moot point?
Who's right here?
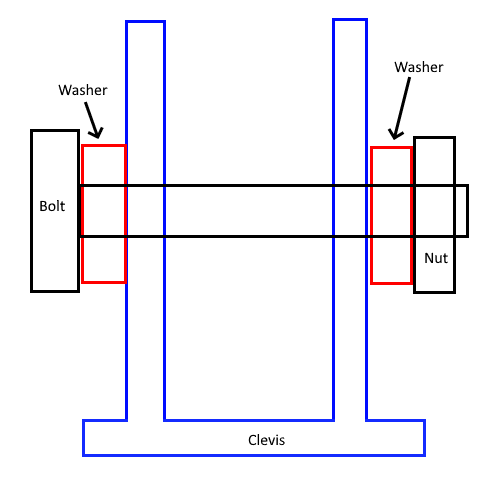
In terms of maximizing the friction, I don't think the washer's diameter matters because friction doesn't care about surface area (assuming a constant pre-load from the bolt and that the washer is always completely covered by the bolt/nut heads for even clamping).
The counter-argument is that with a larger diameter washer, the resistance to rotation is greater since it's a greater moment (the friction is acting further away from the axis of rotation). But surely that's countered by the frictional force being lower throughout making this a moot point?
Who's right here?