1athoti
Mechanical
- Jun 1, 2022
- 14
Hi,
I'm working on a bullwheel capstan system for underground cable pulling.
Can someone give input on whether I'm approaching the loads on the shafts correctly?
From capstan calcs (mainly US Navy wire rope handbook) I'm aiming for 100,000 lbf on final wrap and should be able to achieve it with the 2 sheaves driven by hydraulic motors, geared down etc.
Here I'm considering each individual shaft (both being similar in loading).
The gear shown is driven by another pinion gear with a torque which would create aprox. Wt = 36000 lbf and Wr = 13000 lbf on each gear.
Can I approximate Fpull at center of shaft as 2 x wire rope tension = 200,000 lbf to calculate total loads on the shaft?
Thank you!
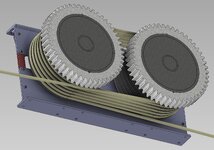
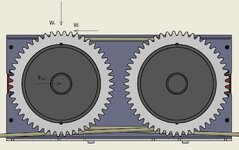
I'm working on a bullwheel capstan system for underground cable pulling.
Can someone give input on whether I'm approaching the loads on the shafts correctly?
From capstan calcs (mainly US Navy wire rope handbook) I'm aiming for 100,000 lbf on final wrap and should be able to achieve it with the 2 sheaves driven by hydraulic motors, geared down etc.
Here I'm considering each individual shaft (both being similar in loading).
The gear shown is driven by another pinion gear with a torque which would create aprox. Wt = 36000 lbf and Wr = 13000 lbf on each gear.
Can I approximate Fpull at center of shaft as 2 x wire rope tension = 200,000 lbf to calculate total loads on the shaft?
Thank you!
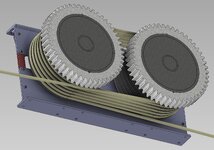
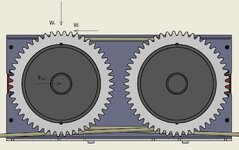