I am working on a project which works on a principle of Dragon whistle simulation (spiral fabric tube linear inflation/straightening inflation caused by Air velocity from one fixed inlet as shown in the attached image).
is this can be done with co-simulation of CFD and structural interaction
or Coupled Eulerian Lagrangian ?
can anyone please suggest me the steps to achieve this kind of simulation
it's great if you can share best suitable tutorial for the same.
is this can be done with co-simulation of CFD and structural interaction
or Coupled Eulerian Lagrangian ?
can anyone please suggest me the steps to achieve this kind of simulation
it's great if you can share best suitable tutorial for the same.
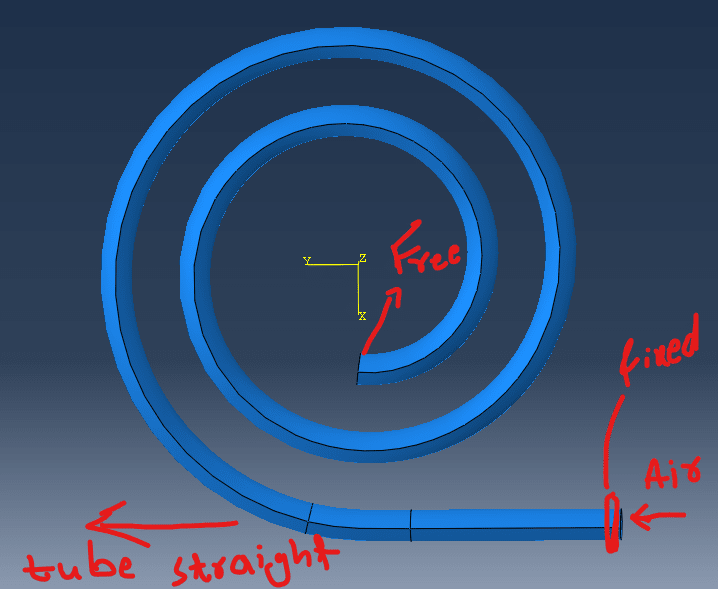