sider
Mechanical
- Nov 26, 2021
- 46
In one of the CHW projects, I had to deal with a cooling unit heat exchanger whose IN/OUT connections were located in the middle of its overall height. After the hydro test, the heat exchanger could not be drained properly, as shown in the picture, as the lower part of it would be flooded since the drain is not located at the lowest point.
Problem
Exchanger Type
Does anybody have any idea how this could be done?
Problem
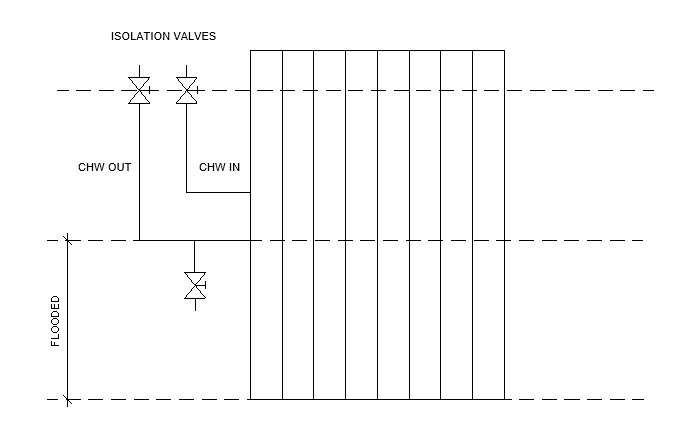
Exchanger Type
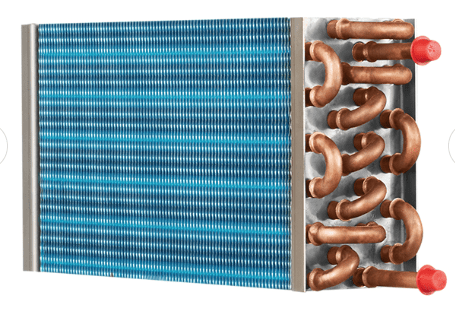
Does anybody have any idea how this could be done?