Below is my study on DRF establishment (for CMM inspection) of different datum options when we want to make a hole a datum feature which has an angle with primary datum plane.
Like to here thoughts from the experts if my understanding is correct.
Overall shape of my part looks like this.
Option 1: Planar primary - Planar secondary - Axis tertiary
Option 2: Planar primary - Planar (inclined) secondary - Axis tertiary
Option 3: Planar primary - Axis secondary
This option locates the DRF far away from the part.
Thanks,
Woosang
Like to here thoughts from the experts if my understanding is correct.
Overall shape of my part looks like this.
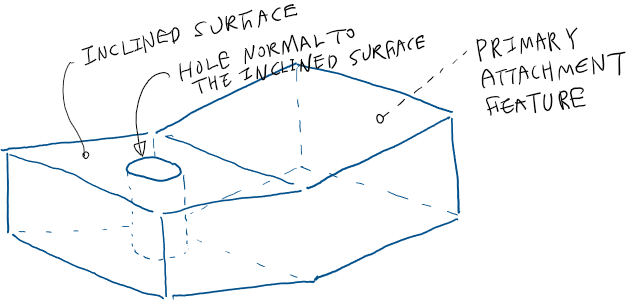
Option 1: Planar primary - Planar secondary - Axis tertiary
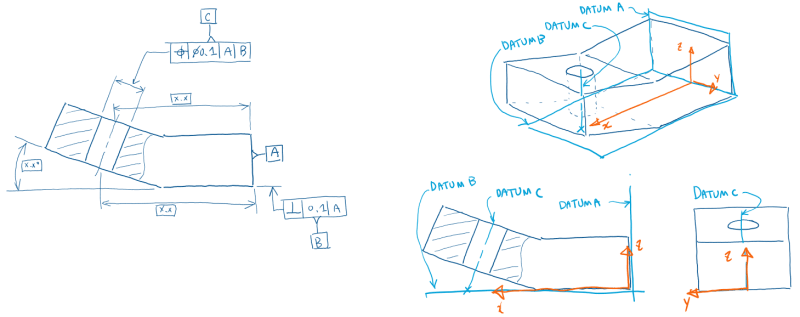
Option 2: Planar primary - Planar (inclined) secondary - Axis tertiary
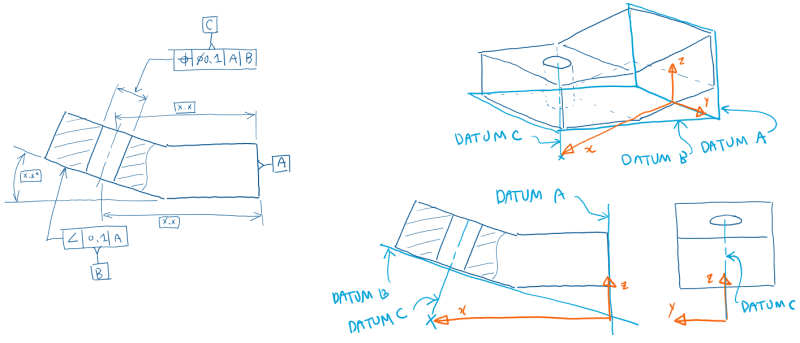
Option 3: Planar primary - Axis secondary
This option locates the DRF far away from the part.
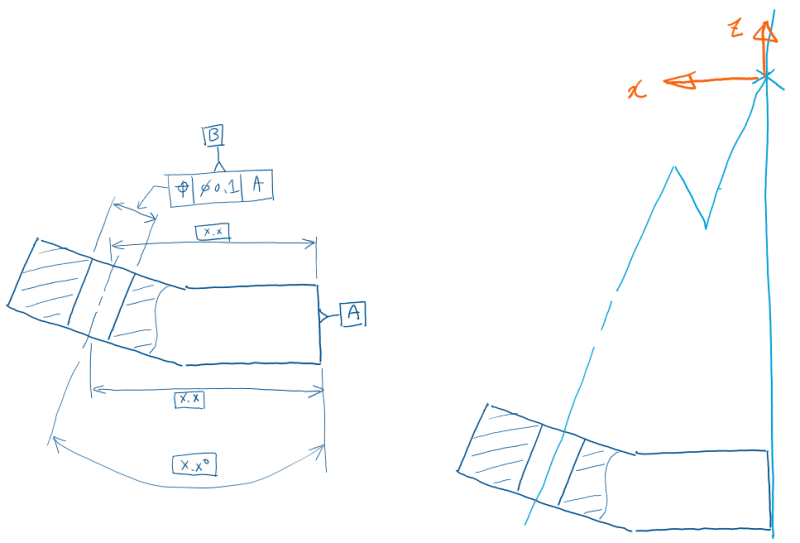
Thanks,
Woosang