Kedu
Mechanical
- May 9, 2017
- 193
Straight forward question:
ASME Y14.5-2018
In order to correcly use dynamic modifier with profile, do we need to have the radius basic or is okay "as-is" (plus / minus)?
ISO
Same question for the OZ modifier.
ASME Y14.5-2018
In order to correcly use dynamic modifier with profile, do we need to have the radius basic or is okay "as-is" (plus / minus)?
ISO
Same question for the OZ modifier.
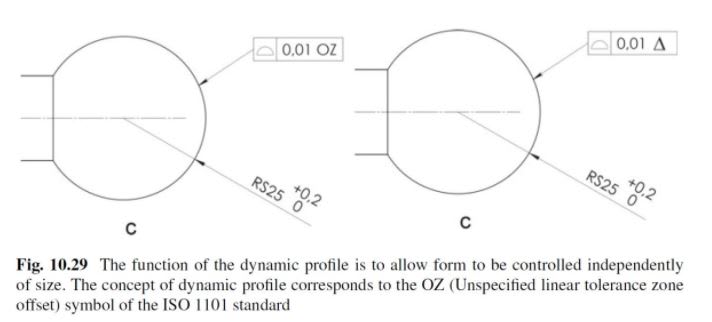