struct_eeyore
Structural
So, I'm apologize ahead of time for resurrecting this topic, but having read thru numerous thread, I'm not sure I've entirely satisfied my curiosity.
In a very typical scenario where we have hollowcore bearing each side of a wide flange beam, but with eccentric loading - the supposed compatibility torsion condition - where is the actual coupling happening that restrains rotation? Specifically during construction before any topping or reinforcing is in place?
The way I've justified it to myself ( see the sketch below ), is that under exaggerated differential rotation, assuming a fully rigid flange, the bearing(s) will shift until they are just points at tips of the cores. With the lighter section being lifted, and its bearing moving further to the outside, the couple is then restored. In field, I assume this all happens with bearing pressure distributions and minimal rotations at the shear tabs. It then remains to check the flange for yield with the point load acting thru the web - at least as an approximate method.
Any and all input appreciated.
As a followup question - if I bear my beam on an embedded bearing plate each end and weld it down (say with fully developed DBAs into concrete), creating some dregree of torsional restraint - would the warping stresses need additional investigation, or would you not consider it in practice?
In a very typical scenario where we have hollowcore bearing each side of a wide flange beam, but with eccentric loading - the supposed compatibility torsion condition - where is the actual coupling happening that restrains rotation? Specifically during construction before any topping or reinforcing is in place?
The way I've justified it to myself ( see the sketch below ), is that under exaggerated differential rotation, assuming a fully rigid flange, the bearing(s) will shift until they are just points at tips of the cores. With the lighter section being lifted, and its bearing moving further to the outside, the couple is then restored. In field, I assume this all happens with bearing pressure distributions and minimal rotations at the shear tabs. It then remains to check the flange for yield with the point load acting thru the web - at least as an approximate method.
Any and all input appreciated.
As a followup question - if I bear my beam on an embedded bearing plate each end and weld it down (say with fully developed DBAs into concrete), creating some dregree of torsional restraint - would the warping stresses need additional investigation, or would you not consider it in practice?
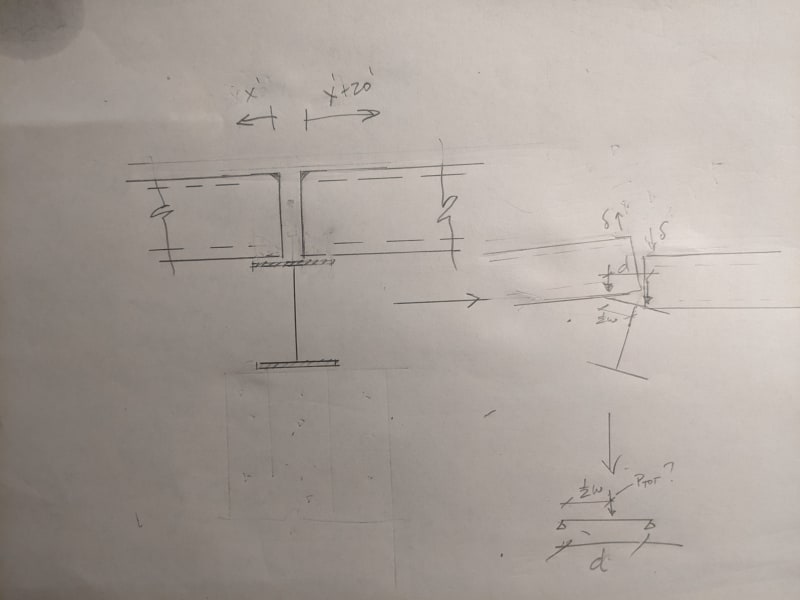