NETDB
Materials
- Nov 10, 2017
- 11
We buy our AISI 4140 material from two different suppliers.
For one particular application we are trying to make a component induction case hardened (since we have the induction machine in house) instead of fully quenched and tempered (which is how we do it today, with a heat treatment supplier). Since the component only requires hardness in the outer areas (>55HRC) it only seems fair to try to do it in house with our induction hardening machine.
The point is, I recently found out that the material from the two suppliers are not provided with the same microstructure. We buy the material from both of them in the "as rolled" condition.
From supplier A you get the picture below (bainite? and perlite from what it looks like) due to unncontrolled cooling. All the material I analyzed from them looks like that.
From supplier B we get the below microstructure (fine perlite and ferrite). I think is odd that we get this microstructure from hot rolled condition without later heat treatment (should be messy microstructure due to uncontrolled cooling like supplier A, in my opinion).
Question is, what is the effect of these microstructures during induction hardening? Meaning: does the microstructure of supplier B favors a deeper case? The initial microstructure of the material matters at all since during hardening it will get austenitized?
The hardness of bulk material from both suppliers are the same. Shouldn't supplier A have a higher hardness?
Also, do you know any good color etchants to differ bainite from martensite using light microscope (without polarized filter or sensitive tint plates)? The ones that I tried with sodium metabisulfite don't seem to work very well.
Thanks!
For one particular application we are trying to make a component induction case hardened (since we have the induction machine in house) instead of fully quenched and tempered (which is how we do it today, with a heat treatment supplier). Since the component only requires hardness in the outer areas (>55HRC) it only seems fair to try to do it in house with our induction hardening machine.
The point is, I recently found out that the material from the two suppliers are not provided with the same microstructure. We buy the material from both of them in the "as rolled" condition.
From supplier A you get the picture below (bainite? and perlite from what it looks like) due to unncontrolled cooling. All the material I analyzed from them looks like that.
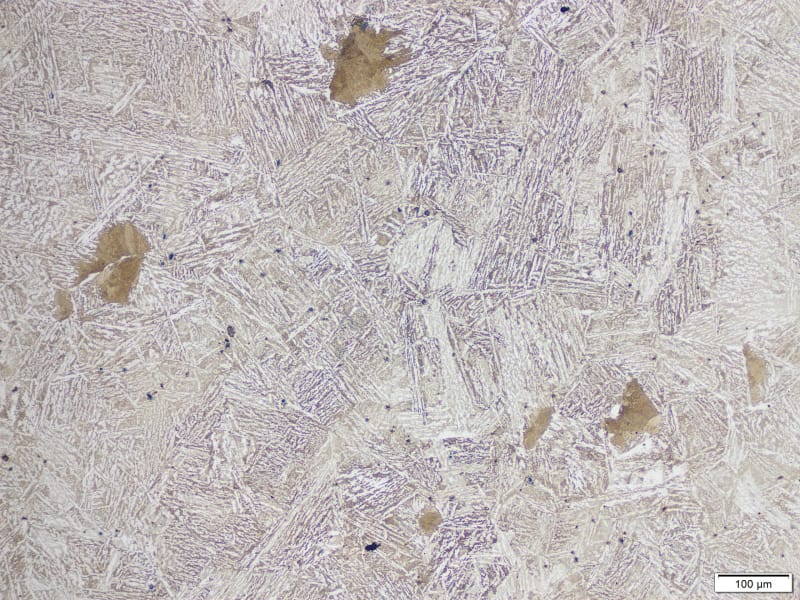
From supplier B we get the below microstructure (fine perlite and ferrite). I think is odd that we get this microstructure from hot rolled condition without later heat treatment (should be messy microstructure due to uncontrolled cooling like supplier A, in my opinion).
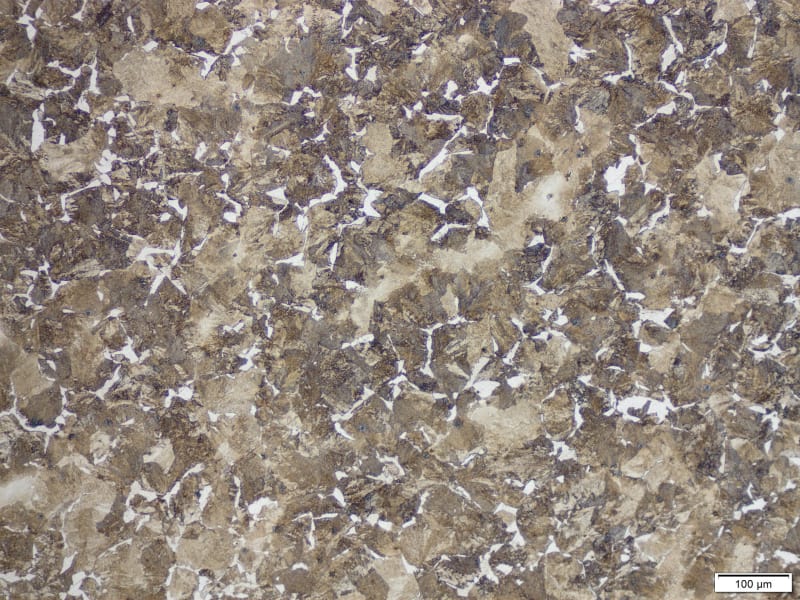
Question is, what is the effect of these microstructures during induction hardening? Meaning: does the microstructure of supplier B favors a deeper case? The initial microstructure of the material matters at all since during hardening it will get austenitized?
The hardness of bulk material from both suppliers are the same. Shouldn't supplier A have a higher hardness?
Also, do you know any good color etchants to differ bainite from martensite using light microscope (without polarized filter or sensitive tint plates)? The ones that I tried with sodium metabisulfite don't seem to work very well.
Thanks!